Tool Selection
Starting your sewing journey with the right tools can make all the difference between frustration and fun! I remember when I first started sewing – having proper tools helped me feel confident and made learning so much easier. While it might be tempting to grab the cheapest options available, investing in quality basics will set you up for success from day one.
Here’s the good news: you don’t need to break the bank to get started! With a budget of around $300-400, you can gather all the essential tools you’ll need to begin sewing clothes. I’ve discovered that many reliable sewing machines, especially from brands like Brother, offer great features for beginners at surprisingly affordable prices – some even under $200!
In this guide, I’ll walk you through the must-have tools that will help you start your sewing adventure. We’ll focus on quality essentials that you can build upon as your skills grow. Think of it as creating your sewing toolkit – one that will support you from your first straight stitch to more advanced projects.
Let’s dive into what you really need (and what you can skip for now) to start creating your own handmade wardrobe!
The Essential Three
When I think of sewing, I think of three stations: Sewing, Pressing, and the Workbench or Cutting Table (which in my case is the same space). So I’m going to cover the three areas and the essentials in each area.
Sewing Machine
Let’s talk about sewing machines – your most important tool for creating beautiful garments!
Before we dive into specific features, let’s talk about the kinds of machines you might run into while searching for a sewing machine. There used to be just sewing machines available for the home sewist. But today, you can buy industrial machines, sergers, embroidery machines, quilting machine and, of course, sewing machines.
When you are just starting out, you do not need a serger. A well-equipped sewing machine will handle everything you need to get started. You won’t be able to do some things as fast. And some stitches won’t look “the same” as ready-to-wear, but there are definitely passable substitutes for the serger stitches.
While machines built for embroidery and quilting can also be used for making clothes, unless you KNOW you’re going to need one of these in the next few years, you don’t need to make that kind of investment. I mean, some of these cost almost as much as my car.
There are two kinds of sewing machines, mechanical sewing machines, and computerized machines, and not all mechanical machines are old. Though the older machines are more often mechanical.
Some of the main differences between mechanical machines and computerized machines are price and functionality.
Oftentimes, the mechanical machines are a little bit less expensive than the computerized machines. But you tend to get more features on the computerized machines that can make certain tasks easier, especially in garment sewing.
One of the benefits of computerized machines is that they can have more force at lower speeds. That means the computerized machines can push the needle through the fabric at a much lower, and therefore safer, speed. The mechanical ones will rely on momentum to get through tough fabrics. I used to find myself sewing really fast before an increase in thickness just to get my old mechanical machine to keep going through it.
With my computerized one, if it can’t push the needle through, it just stops and then it resets itself. It doesn’t have any momentum to keep trying. So, where I’ve broken a bunch of needles on my mechanical machine trying to force it through thicknesses, I haven’t on the computerized one.
Truth be told, I haven’t used many modern mechanical machines. So, they may behave better than my 1975 mechanical one does.
If you’re brand new to sewing. Another feature that I think is good for new sewists, especially if you’re a little apprehensive about the machine is a slow sew option. I don’t know how many mechanical machines have that option. I do know that a lot of the computerized machines will have a slow sew setting, or maybe a slow speed setting. Some machines may have a dial or a lever that you can manipulate to regulate maximum speed. Or, they may just have a button that turns the feature on and off.
If you’re just starting out and don’t really have the means to buy “big”, you can get a machine that will do the critical functions for under $100. But you may outgrow it quickly.
That being said, if you can swing a little more, you can get some pretty cool features in the $250-500 price range. And not outgrow it for a long while.
You should also look for a full-size machine. Even full-size machines can be portable, if you need that.
Essential Machine Features
There are some machine features that I would consider essential for making clothes. If your machine has these, you can sew almost anything even if you have to manually make certain stitches. (Like a buttonhole).
If you are looking for a machine, these are the must-haves. If you already have a machine, check to make sure these features exist, if not, consider purchasing a new one. (Hint, most modern machines will have these key features unless it’s an industrial machine.)
Stitch Features
These are the critical stitches your machine needs for you to adequately sew clothes.
- It must make a straight stitch.
- It must be able to go in reverse.
- It must be able to make a zig-zag.
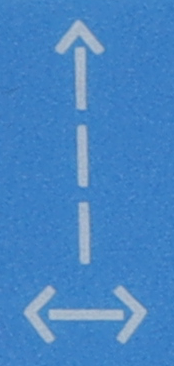
Straight Stitch Symbol
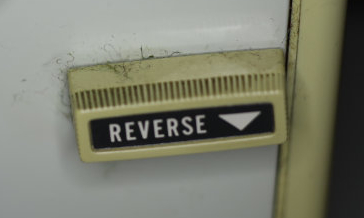
Reverse Lever on Sewing Machine

Zig-Zag Stitch Symbol
The straight stitch is the most used stitch on the machine. You’ll use this in almost every garment you make, even the stretchy fabric garments.
The machine must be able to go in reverse or “backstitch”. This is what will lock your stitches to they are less likely to pull out when wearing the garment.
And a zig-zag stitch will be your go-to stitch for finishing edges on woven fabrics, and making stretchy stitches for knits (activewear or close-fit body suits).
Between the zig-zag and straight stitch, you can do many different types of stitches manually like basting, buttonholes, bar-tacks and satin stitches (like for appliqués). Depending on what you are going to sew, you will likely want far more stitches than just a straight and a zig-zag.
And be aware that some inexpensive machines boast of having 17 stitches, but it’s just using the following adjustment features and combining them with the straight stitch and zig zag stitch to create half the stitches.
One more thing to note, if you are planning on sewing activewear like leggings, sports bras, leotards and such, you will want a machine that has an overedge or overcast stitch. This is essential for making seams that stretch and don’t pull apart or break on close-fit stretchy garments. Do not confuse the symbol for the overedge stitch with the symbol for a blind hem stitch. A blind hem stitch will not work for sewing stretchy fabrics.
Adjustment Features
There are a bare minimum of adjustments you’ll need to be able to make on your machine as well.
- Thread Tension Adjustment
- Stitch length Adjustment
- Stitch Width Adjustment
You’ll need to be able to adjust the thread tension to allow for thickness differences in fabrics, and thread. But also, this is an easy way to create a basting stitch. Note that usually only the top thread has a dial adjustment for tension. The bobbin thread might be adjustable but usually requires a little screwdriver and isn’t a very precise adjustment. In that, there’s no dial or numbering system to know how much bobbin tension you have.
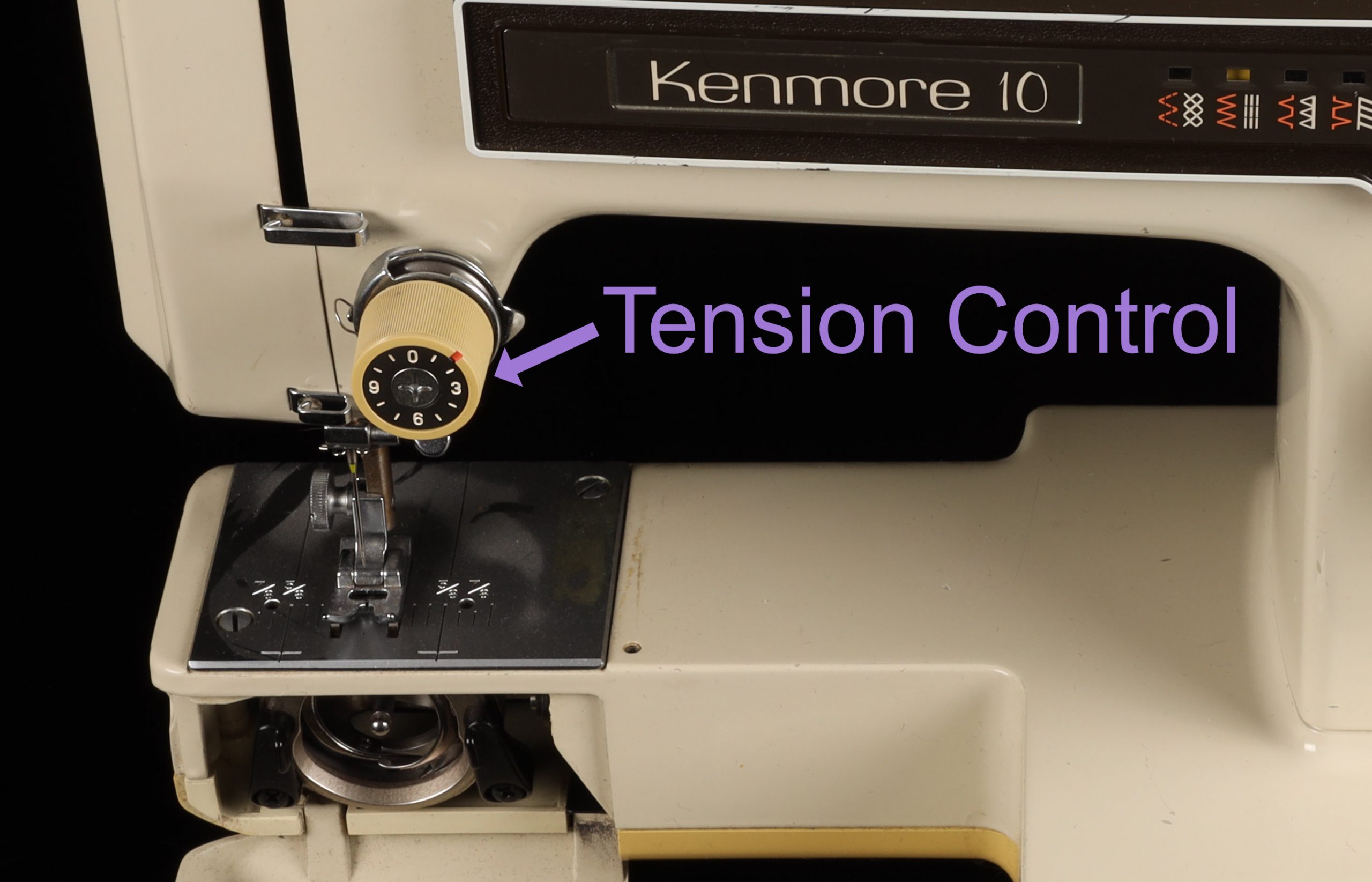
Tension Control Dial on Sewing Machine
You’ll want to be able to adjust the stitch length. This is how much fabric is pulled through the machine before the needle goes down again. Heavier fabrics often look better with longer stitches. Also, some fabrics don’t hold up too well with a lot of needle punctures, so a longer stitch is good. However, if you are doing a satin stitch or button hole, you’ll need a much shorter stitch. Often, top stitching or edge stitching will have a longer stitch than what was used to construct the garment.
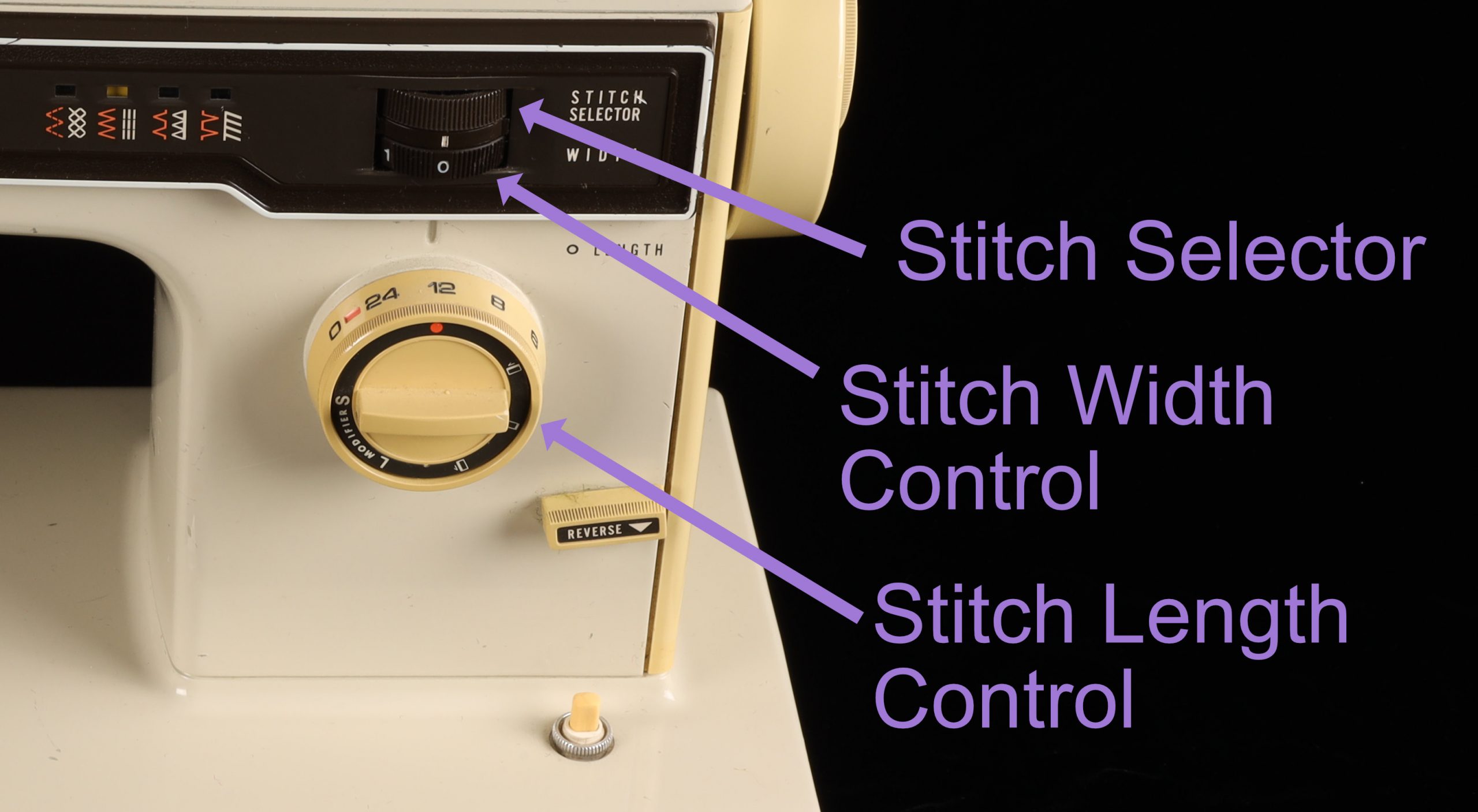
Stitch Control Dials on Sewing Machine
Width adjustment applies to zig-zag type stitches (where the needle goes side-to side). Adjusting the width helps for a variety of stitches. Buttonholes would want a much narrower stitch than something you’d use to finish an edge in the seam allowance.
Again those cheap machines will have a narrow zig-zag and a wide one, and a short one and a long one. Then, to create a buttonhole, you’ll use the narrow, short zig-zag on the left, the narrow, short zig-zag on the right, and maybe a wide but short zig-zag on the top and bottom. That’s 3 stitches on there and you’re limited to the preset settings of each of the stitches. So you wont’ have as much adjustability to accommodate a variety of fabrics and applications.
Accessories
Another thing to look for is the ability to get a variety of feet for the machine. There are a few feet out there that make life easier.
Your machine will likely come with a standard foot to use with straight and zig-zag stitches.
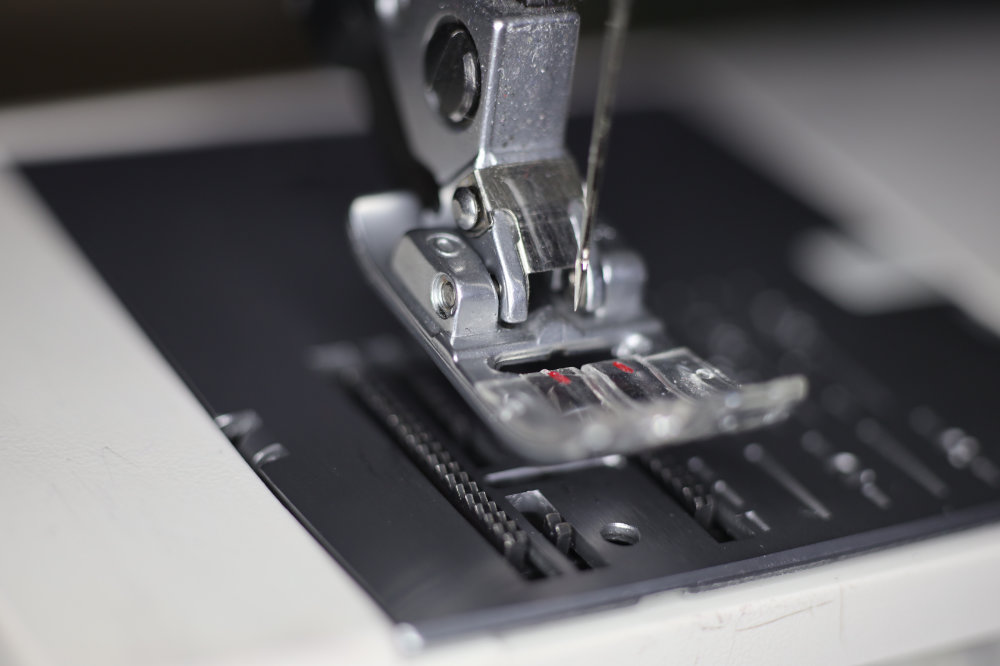
Standard Foot with Zig-Zag Capability on Sewing Machine
The next most common foot would probably be the zipper foot. This foot allows you to get your needle way close to the teeth of the zipper while still holding the fabric down.
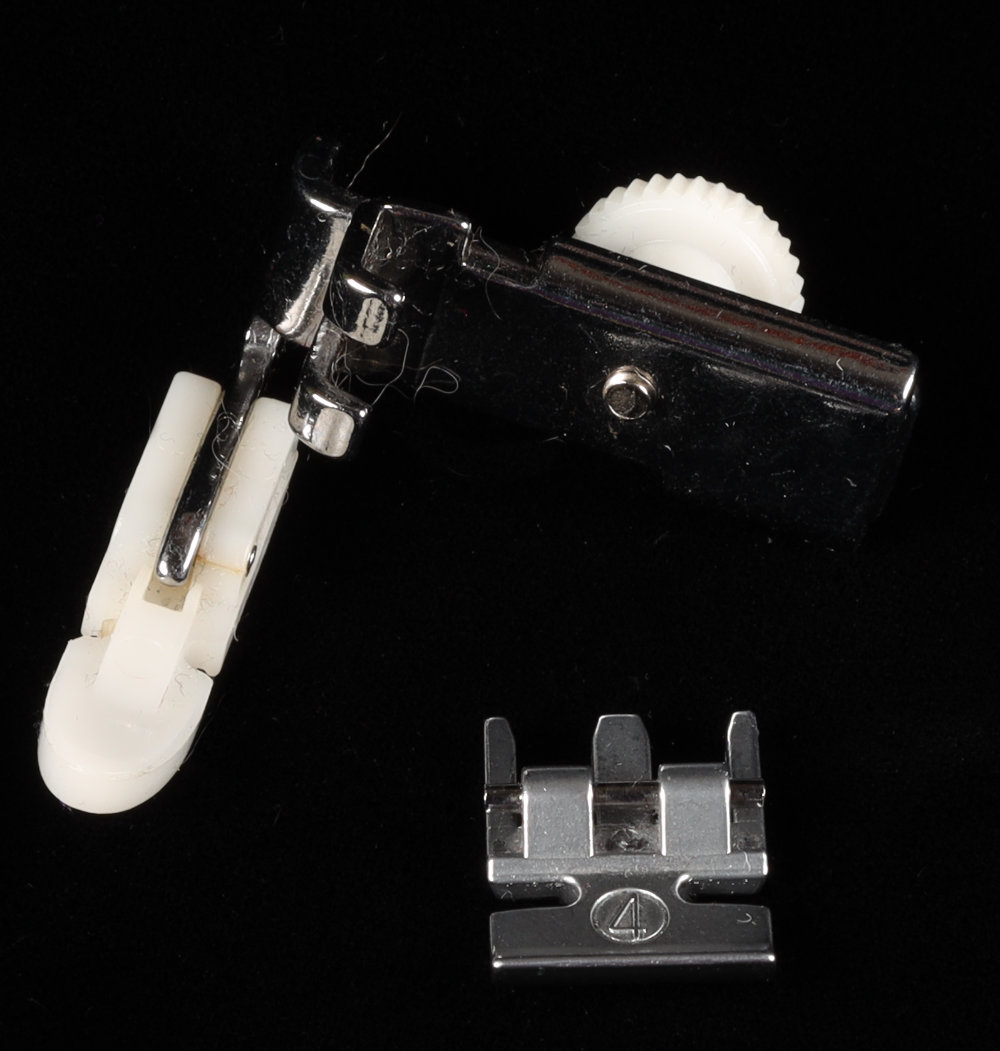
Two Styles of Zipper Feet for a Sewing Machine
Even if your machine doesn’t come with a bunch of feet, it’s good to have the option to buy feet for it. Some use a standard method of foot attachment and others are more proprietary. It’s best to check with the manufacturer on it. If it says something like “click installation” the mechanism may be proprietary. See the sidebar for useful attachments and accessories you may want to spring for or verify are available for future purchase on your machine.
Nice-to-Have Features (Budget Permitting):
While you can get by with a very basic machine as indicated above, there are some features that make life a lot easier when sewing, especially if you are sewing clothes. These aren’t strictly necessary, so weigh your options and splurge if your budget permits.
Function Extras
Here are some cool functions that you may want to consider springing for.
- Stop with Needle Down – For my sewing needs, this is pretty much a must-have feature. Now, you can get away without it, so if it’s not in your budget, you don’t NEED it. But it’s really nice. Here’s the thing, when you’re sewing long seams, you have to stop and reposition your hands and such every so often. When you do this, you don’t want the fabric to shift under the presser foot. So, if you stop with the needle down, you can guarantee that part won’t slip. Also, if you are making corners, you need to stop with the needle down and pivot. If you can get a machine with this (if it’s in your budget), I highly recommend it.
- Manual or automatic needle threader – This one is an interesting feature. My machine has a manual needle threader. It’s really neat. But it doesn’t work really good on tiny needles like size 8. I’ve also broken mine, twice. That being said, I love it and when it doesn’t work (or when I break it… don’t ask) I miss it.
- Presser foot tension adjustment – I’m tossing this in here because some machines call out that they automatically adjust the tension of the presser foot according to what you are sewing. This is good. If not, make sure there is a way to adjust the pressure. Too light of tension, means your fabric will slip around more and not feed through very well. Too much tension will prevent the fabric from feeding well, and on some fabrics could cause the presser foot to mar the surface of the fabric. And, incorrect pressure may affect stitch quality.
Stitch Extras
I remember way back in the day as I was JUST starting to learn to sew. My mother had an old machine (I don’t even know what brand). And it was all mechanical and manual. I don’t actually have any memory of using it, but I do remember playing with the boxes of cams that the machine came with so it could do some of the stitches. Nowadays, we can just poke a button or turn a dial and the machine electronically (or mechanically) automatically changes the stitch. And lots of stitches are quite complicated. Imagine needing to install a set of cams in the right order and placement just to get a specific stitch.
My mother’s replacement machine had a stitch that formed a little train, just the engine and coal car. How cute. The machine I have today does letters. Truthfully, I bought the machine for the buttonhole. Too many machines I found at the time were focused on quilting. I don’t quilt. But for sewing clothes, I need an automatic buttonhole stitch.
Here’s a list of cool stitches that I’ve used quite a bit in my garment construction. This isn’t an order of importance. Note that there aren’t that many. Some machines offer 70 or 100 built in sewing stitches. Most of them are likely decorative. Which you may, or may not, really need.
- 1-step automatic button hole – If you are going to sew clothes, I HIGHLY recommend that you buy a machine that does this. Yes, most machines will at least do a buttonhole that requires your involvement. But It is so much more efficient, and fun, to set up your machine and fabric, then just hold the pedal down and let it go. If you are making a button-down shirt, you will have to do a LOT of buttonholes. Making them in 2 to 4 steps would be a pain in the butt. But do you NEED 7 different button holes? No… I mean, you could get away with just the standard rectangular one. But, if more is in your budget, go for it. Here’s another use I have for buttonholes. I use them for the opening on waistbands for drawstrings.
- Stretch Straight Stitch – This stitch looks like a really thick straight stitch. But, it’s formed in a way that it stretches after sewn. I wouldn’t use this for sewing activewear because it just doesn’t stretch enough, but I have used this stitch to make a thicker looking straight stitch and for seams that need give but not too much stretch.
- Lightning Stitch – This stitch is similar to the straight stretch stitch but has more width. It also stretches more. And looks like a bolt of lightning.
- Button Attachment Stitch – This stitch can be used to attach buttons (the flat 2 or 4-hole kind, not the shank kind). But it also can be used to do a small tack stitch to hold something in place. You could also accomplish this with a zig-zag with stitch length set to zero, so don’t pay more JUST for this stitch unless the machine also has the ability to have a foot to hold the button while doing the button hole stitch. And you think you’re going to sew a TON of buttons on.
- Invisible hem stitch – This stitch is used to automatically create an invisible hem. You can use it along with your invisible hem foot, but you don’t need the foot. Again, this is super helpful to replace hand stitching. 🙂 I’m a huge proponent of using the machine instead of hand stitching. And I think this stitch is probably in my top 5 must-haves for sewing clothes.
- Overlock stitch(es) – I’ve already mentioned this as a must-have if you’re sewing activewear, but I’m putting hit here also. My machine has at least 3 stitches that I can use to replace an overlock stitch that would require a serger to create. While your sewing machine won’t trim the seam allowance, these faux overlock stitch options are great to use, especially on 1/4″ seam allowances which are becoming more common on patterns for activewear or stretch fabrics. You might see the term overedge or overcast in the manual. And Mine has some stitches that are essentially overcast type stitches but are called something completely different but the description says “for seams that stretch”.
- Elastic Stitch – This is a straight stitch made into a zig-zag pattern. Its super useful for sewing all kinds of stretchy stuff, elastic, hems on shirts, and even some seams.
- Automatic Bar-tack stitch – This is a great stitch to use for creating a bar-tack. You’ll find bar-tacks on jeans pockets and such. They reinforce areas of garments that can be under more stress like the tops of pockets. You can also use it for reinforcing the attachment of accessories like swivel hooks, d-rings, key chains and such. You can make one of these manually, so if the machine in your budget doesn’t do this, it’s probably the least important of all the stitches on this list.
Accessory Extras
Some machines come with a bunch of additional feet or accessories. As you sew more and more, you will come across times you want more than the standard presser foot. Also, you may find the need to swap out other parts like the working table to be larger (for better control of the garment as you’re sewing it). Here are some accessory type features you may want to consider. Even if your machine doesn’t come with these, you may choose to buy a machine that specifically has some of these options available for future purchase, if you see yourself sewing something that would benefit from the accessory.
- Invisible zipper foot – If you think you’ll be sewing a bunch of invisible zippers, you can get one of these. It’s specially designed to fit with the teeth of the invisible zipper so that you can get really close without making the zipper inoperable. Most machines will have an option to buy this as an add-on later, even if it doesn’t come in the box.
- Stitch in the ditch foot – The stitch-in-the-ditch foot helps you guide your work under the foot in such a way that sewing a “stitch in the ditch” is way easier. It can be used as a guide for other things as well.
- Blind Hem foot – The blind hem foot gives a guide for machine stitching blind hems. It’s quite useful since on a blind hem you need to only pick a single thread from the part that would be seen on the front of a garment. (Blind hems are often used to hem pants and skirts.) Note that while I use the blind hem a LOT, I rarely do it well enough for it to really be blind. But you know, if someone is hanging around the hem of my pants, they have issues.
- Straight Stitch Needle Plate (and foot) – This presser foot and needle plate is used when working with super light fabrics like chiffon and charmeuse satin. It helps prevent the fabric from being pushed down into the bobbin area of the machine especially when starting stitches. It’s useful, not a must-have. And it’s critical that if you are using this, you remember to switch back to the regular needle plate to do wider stitches like a zig-zag stitch.
- Large Work Table (or add-on option) – When sewing garments, you really want to be able to feed the fabric through your machine in a nice even and controlled way. Some machines come built into a table (especially the older ones) where the needle plate is level with the table surface. The thing is, most modern machines aren’t set up to be furniture. And lots of home sewists don’t really have a space dedicated to sewing that could have a piece of furniture with an embedded sewing machine. Some machines come with a large work table or work surface. Some have options to buy an additional extension for your machine. And actually, you can find them online to fit any machine.
- Larger Work Space – This is the distance between the needle and the body of the machine. If you plan to sew quilts, blankets, or drapery this could be a useful feature.
- Walking foot – Some Machines have an integrated walking foot device that you can engage or disengage, rather than a separate foot that you have to take on and off. A sewing machine has feed dogs that pull the fabric through the machine. Feed dogs are only on the bottom, affecting mostly just the bottom fabric, the top fabric is left to glide under the foot. A walking foot helps pull the top fabric through as well. A walking foot helps, but it will never pull quite as much as the feed dogs.
Features You Can Skip
If you find yourself looking at a machine that is just out of your budget, but has some of these features that look amazing. Keep in mind that for most sewing you won’t need these.
- Decorative stitches – You’ll rarely use these for basic garment construction. Sure, they are fun. I’m going to lump quilting stitches in here if you don’t plan to quilt. And I’m going to add heirloom stitches here too, if you don’t see yourself doing heirloom sewing.
- Built-in embroidery features – Again, like the decorative stitches, you won’t need these unless you specifically want to do embroidery.
- Free-Arm Option – Most machines have the option to remove part of the work table to give you a smaller free-arm. Many resources consider this a must-have. But you don’t need it. In fact I don’t use mine now at all. And I still sew small hems and other things in the round.
- Automatic Tie-on/Tie-off – When starting and stopping a stitch, the recommendation is to backstitch one or two stitches to “lock” the stitch. Some machines now come with a button you can press that will basically do this for you. I literally just discovered that mine has it (I’ve had my machine for over 10 years). I’m still trying to get into the habit of using the feature. I’ve been sewing for 30+ years without the feature, and backstitching is a habit. (In fact I have to really think about not doing it when making basting stitches that I need to pull out later.)
- Automatic thread cut – some machines come with the ability to cut the thread off for you. It’s convenient, but not something you need. It would technically reduce the amount of thread you use because you wouldn’t have to pull as much to get at the threads to cut. Plus the tails would be shorter when starting. I’ve lived without this feature for over 30 years. But if you see it now you know what it is. It could significantly reduce the amount of stringy detritus in your sewing space (a good thing if you have cats).
- Knee lever for presser foot lift – this is a function for the hard-core sewist. In order to sew, you must lift and lower the presser foot. Lifted allows you to put the fabric in and take it out. But the machine doesn’t make a good stitch with the foot lifted, so you have to lower it to start sewing. Having the option to lift the foot with your knee would free up your hands to place the fabric under the presser foot without wishing for a third hand. However, this feature also requires a more dedicated sewing space. The lever would have to go through the table your machine is on. So, it’s not an option if you sew at your dining table.
Remember, your perfect machine depends on what you plan to sew. If you’re focusing on garments, features like a one-step buttonhole and needle down position might be worth the extra investment. The key is finding a reliable machine that matches your sewing goals and budget!
Pressing and Ironing Tools
Let’s press on to one of the most crucial tools in sewing – your iron! A good iron can make the difference between professional-looking garments and, well… something that screams “homemade.” While I use a specialized iron now, there are several excellent options for beginners.
I’m going to start off by saying that there is pressing and there is ironing. I know it’s splitting hairs. But really you can think of it this way: Ironing is used to take wrinkles and maybe creases OUT of your fabric, and pressing will put creases IN your fabric and help shape your garment or finished project. And because of that, there are more tools for pressing than there are for ironing. But they do overlap.
Iron
As much as I hate to admit it, pressing while sewing is crucial for making your finished project look “handmade” in a good way, not “homemade” in a bad way. You will want a good quality iron (and don’t skip any of the ironing or pressing steps in your instructions!)
And, like I said, I use a “specialized” iron, which is a gravity fed iron that has a separate container for water that I hang from my ceiling, you don’t need to go that far, especially if you are just starting out or you live somewhere that you can’t hang iron water jugs from your ceiling.
You will want these features on your iron though.
- Heavy base
- Good steam output
- Multiple heat settings
- Sharp, pointed tip
It might seem like it’s a good idea to have a light-weight iron. But a heavier iron means the iron can do more of the work without you needing to add your own muscle.
And you will likely want steam. A good iron will have a large enough reservoir that you aren’t constantly filling it up. And a larger reservoir will add to the weight when full.
Most irons will have multiple settings for different fabrics. Check reviews. Irons that have good steam output will do so even at lower temperature settings. Some irons don’t get hot enough to really make steam, and they will leak water onto your project. This is not only frustrating but could ruin your project.
And the last feature to really look for is a pointy tip. That will help get into corners and tight spaces when pressing.
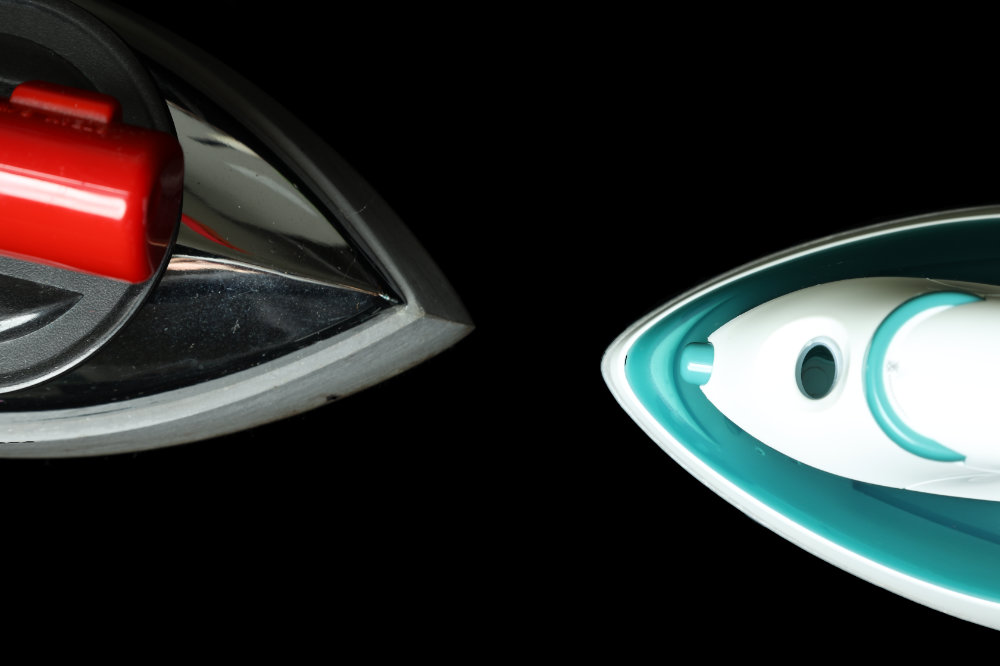
Comparison of Iron Tips (Pointy on the Left)
Pressing Surface
In order to save your table or countertop, you will want a surface specially for ironing or pressing on.
The most common option the an ironing board that has X-shaped legs and one squared off end and one end that narrows into a rounded almost point.
While they range in size, I would consider this a full-size ironing board.
Here are some things to look for if you have the space and budget for a stand-alone ironing board:
Adjustable Height
Make sure that you can set the height of your board to a good height for you. You don’t want back, neck or arm strain when pressing. Remember, if you have a heavier iron, it’s going to do the work, but moving it about if the board is too high will eventually lead to physical discomfort.
Removable and Washable Cover
I’m not going to lie. There is a very good chance that at some point, you will want to remove your cover, and maybe even wash it. Now, you could go your whole sewing life and not do this. But, if you’re like me, you’ll get something on it you want to wash off. (Can anyone say “fusibles”?). And if you sew a lot, and your cover wears out, you can sew yourself a new one.
Sturdy Base
You want your ironing surface to be sturdy. No one wants an ironing board with a hot iron tipping over and causing injury or damage. Look for wider bases.
Wide Pressing Surface
This need can vary based on what you primarily sew. But for ironing fabric, the larger the surface the better because you have to move the fabric around less when ironing. Of course, bigger does mean more space to store it. So there may be a tradeoff needed.
And that brings me to some space-saving options.
Pressing Surface Options:
While a full-size ironing board is ideal, there are several space-saving alternatives:
- Tabletop ironing boards – Perfect for small spaces
- Over-door ironing boards – Great for apartments
- Wall-mounted fold-down boards – Space-efficient solution
Additional Pressing Tools
There are a few tools or notions that you may want to consider beyond the iron and ironing board.
You can get started without these. But keep in mind some of these options, especially knowing what you plan to make.
Wooden Clapper
If I had to recommend only ONE additional pressing tool it would be the clapper. If you want to make crisp creases in your fabric when pressing the clapper is your friend. I can’t stress enough how good pressing will turn your project from amateur to professional looking. Well, a clapper will help you get all sorts of good pressing results with a lot less effort. And it will help cool your pressed pieces faster so you can pick them up and work on them sooner. Within reason.
Point Presser
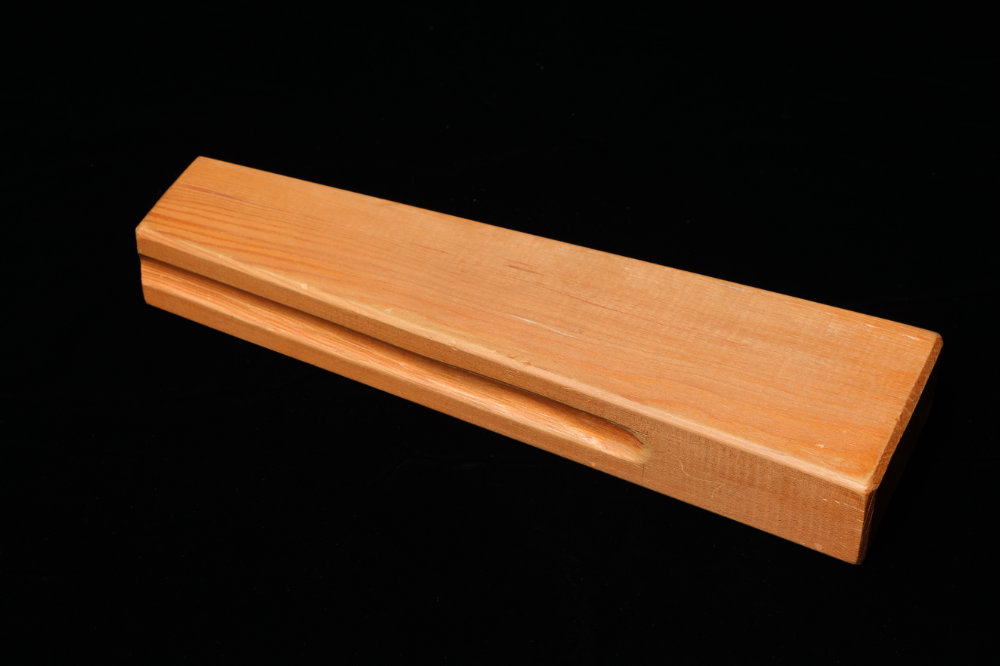
Wooden Clapper
A point presser is a tool that has a bunch of points and curves that you can put parts of your project over and use to press seams open in a variety of shapes. I used mine extensively for sewing my form-fitted facemasks during covid. And I use it a LOT when making bags and purses to get into corners. Some point pressers have a tiny clapper as well, but I don’t generally use mine unless I absolutely need an extra one for something. It’s kind of small and needs to be sanded.
Tailor’s Ham
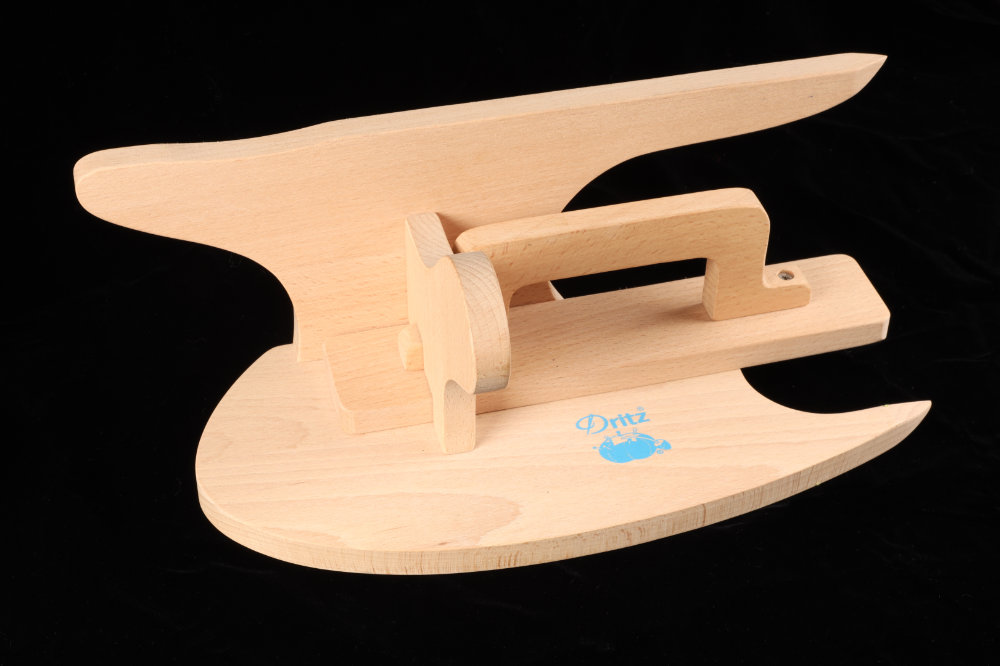
Point Presser (With Integrated Clapper)
A tailor’s ham is a VERY useful tool if you are making curved things. So, again, maybe not the first thing you buy, but I use mine for sleeves, face masks, bra cups, shaped darts, some pants hems and probably a bunch of other things I’m not thinking about.
Seam Roll
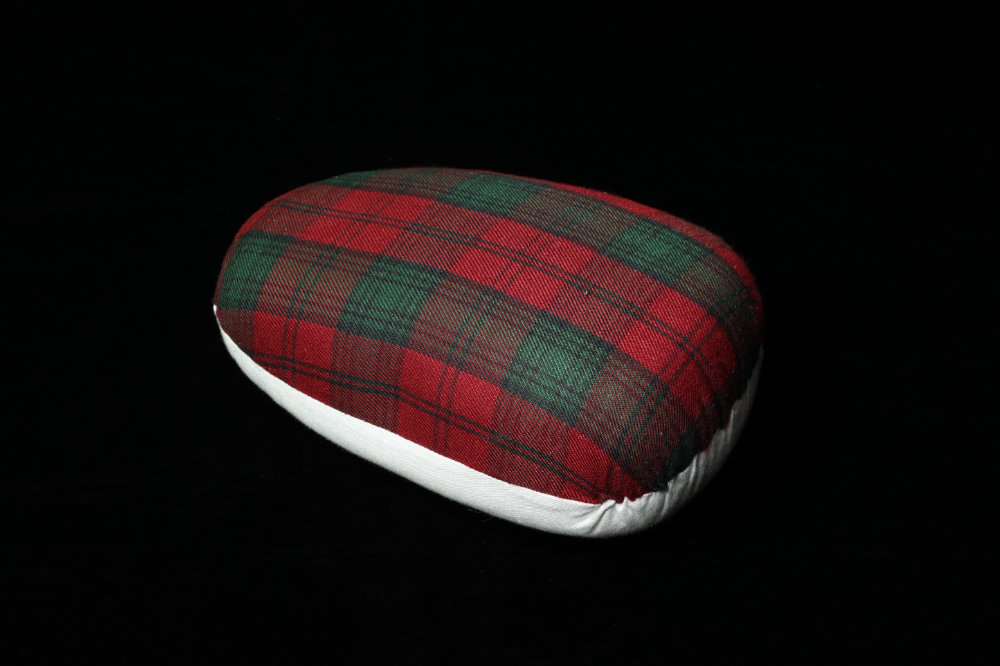
Tailor’s Ham
A seam roll is a long stuffed tube that is quite useful for pressing seams open on straight seams. It helps reduce the ridges that can sometimes show through to the front side of the fabric. I also use mine extensively when pressing up hems for my leggings. And I will use it to press up hems for shirts sometimes if I just can’t get the layers to be separate and I need to not crease the back when pressing the front or vice-versa. And it’s great if you’re dealing with long sweeping curves on hems like you sometimes find on shirts and maybe some skirts and wide-leg pants.
Sleeve Board
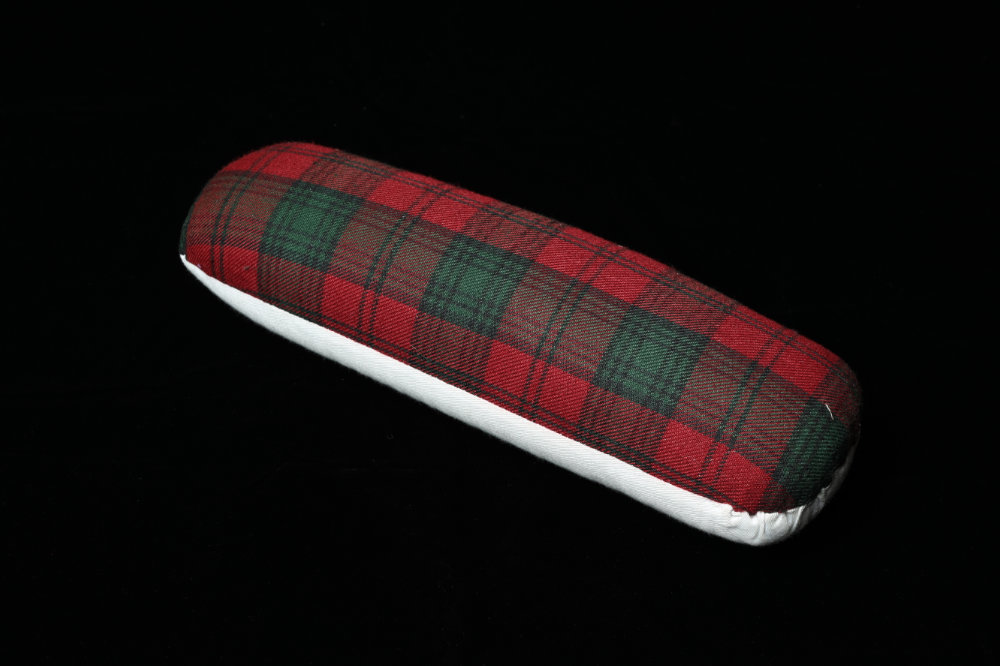
Seam Roll
A sleeve board is more for pressing finished seams after they are assembled to the garment. They can also be used for pant legs, but are typically not long enough for an entire leg.
They are narrow enough for a typical shirt or blouse sleeve to slide over it and provide a much better option for pressing sleeves than the tapered end of your ironing board.
Press Cloth
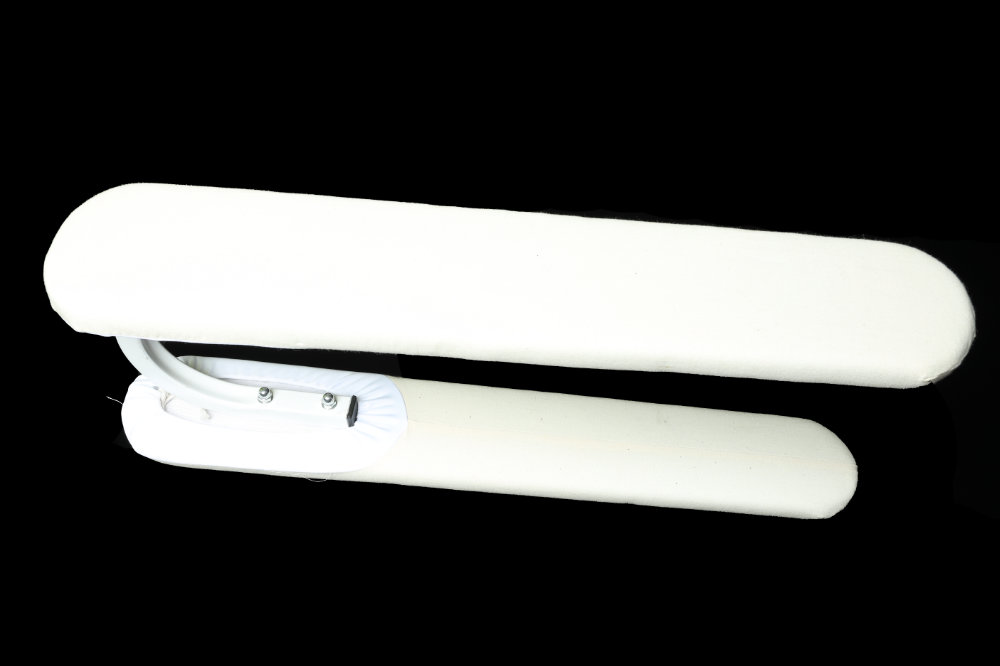
Sleeve Board
Some folks will tell you that you absolutely need a press cloth. And you do, if you’re sewing delicate fabrics and you need to protect them. OR, if you are using fusibles and want to protect your iron or ironing surface cover. But, for protection of the surface you can use a towel or something you already have.
If you are just starting out sewing, I don’t recommend starting with expensive fine fabrics that would require a press cloth. Just because if you make a lot of mistakes it’s more expensive and heart breaking. But, do get a press cloth if you think you’re going to want it to protect the iron from fusibles. Personally, I just clean my iron after I get sticky stuff on it. Otherwise I’d have to keep track of what side of the press cloth has all the fusible stuff on it.
There are also 3 (at least) different kinds of press cloths. And they are all for different uses. One thing they all have in common is they are very heat resistant. So, if you need one in a pinch, you can get by with some scrap fabric that fits the bill.
Remember, you don’t need every pressing tool right away! Start with a good iron and ironing board, then add specialized tools as your projects require them.
Notions
The third “thing” you need of the “essential three” are specific notions that aren’t for pressing specifically. We can break notions into two sub-groups: Long-lasting Tools and Consumables.
As with the pressing tools, there are some you need right away, and some you may want to get sooner rather than later depending on your sewing projects, and then some that you may never really need.
I’ll cover tools first, and then consumables dividing them each into Must Have, Nice to Have and Extremely Project Specific Probably.
Long-Lasting Tools (or Notions):
I’m calling these long-lasting tools because with proper care and storage they can last a very long time. However be aware that they can break, or distort, or just need to be replaced at some point in the future.
Must-Have Tools
There are 3 tools I consider to be essential if sewing. Though you can probably get away without the third, you really shouldn’t try if you are going to make a lot of clothes.
Fabric Scissors
You will need some way to cut your fabric, and even if you really want a rotary cutter and mat, you should still invest in a good pair of fabric scissors because they will be used for lots of things you cannot use a rotary cutter for.
Look for longer scissors (about 8″). You’ll be able to make straighter cuts with the longer blades. You can also cut smoother curves with longer blades.
Also, look for something with a comfortable handle. You want to be able to fit your thumb and the fingers of your hand into the handle without cramming them in.
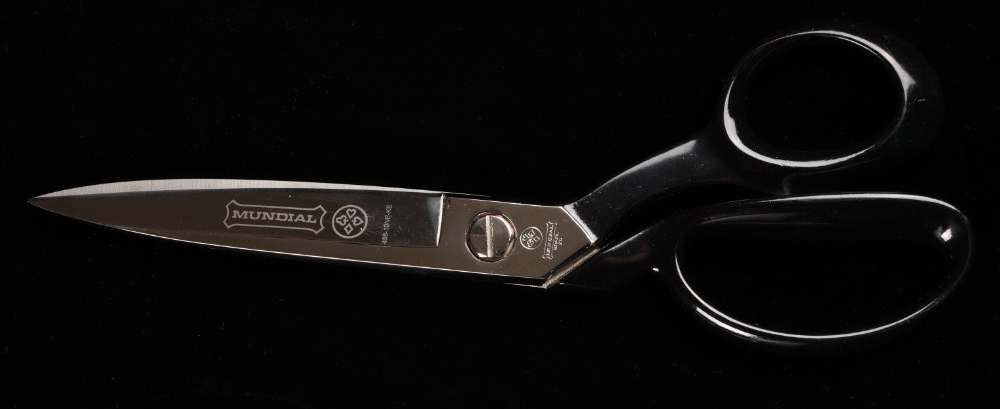
Fabric Scissors with Long Blade
The heavier the scissors the more fatiguing using them will be. If you have smaller hands or hand issues such as arthritis, some brands feature spring-loaded scissors. This means you can relax your hand to open them and only have to flex to close the blades.

Fabric Scissors with Spring-Loaded Handle
A good pair of scissors should last a long time. Eventually they will wear out, but you can get a good decade or more out of them if you take care of them.
There’s a thought that you can’t cut paper with your sewing (fabric) scissors. The theory is that it will dull them. The reality is that all scissors will eventually dull, even cutting fabric. There are far more insidious things you can do to your scissors that will make them dull or cut poorly than cutting paper.
Here are 3 tips to keep your scissors sharp:
- Don’t drop them! For goodness sake, don’t drop your scissors. It’s unsafe. You could stab your foot. But also, when they land, the blades will hit together and could cause gouging of the blade. Small nicks or chunks missing from the blade results in spots that won’t cut through fabric.
- Don’t Cut Metal! Be careful when cutting out your patterns, if you’ve pinned the pattern to the fabric, take extra care to make sure the pins don’t extend over the cut line. Also, if you are sewing a zipper with metal teeth, and you need to cut the length of it, be mindful of where you are cutting. Try to cut between the teeth. Or, be safe, and only cut the tape with your good fabric scissors and then use an expendable pair of scissors or kitchen shears to do the metal part.
- Be Mindful of what they are used for. Yes, you can cut paper with your fabric scissors. But don’t use them excessively for things outside sewing. Don’t use them as kitchen shears, don’t cut your cardboard boxes and packing tape with them. Don’t cut carpet. And if you are going to be using really thick paper like tag board, consider using other more expendable scissors. Keep your fabric scissors clean and in your sewing room (or basket or whatever you keep your sewing stuff in).
Seam Ripper
Often, new sewing machines will come with a Seam Ripper. But if your machine was used or a hand-me-down, you may need to purchase this.
And you may want to purchase a new one anyway if the one that came with your machine is not comfortable in your hand.
And while it’s all well and good to think that you won’t need one, it’s really the best tool for the job of seam ripping. And yes, you’ll likely need one at some point.
There are other things seam rippers are useful for, other than undoing erroneous stitches. For example, it’s one of the best tools to remove basting stitches.
Measuring Tape
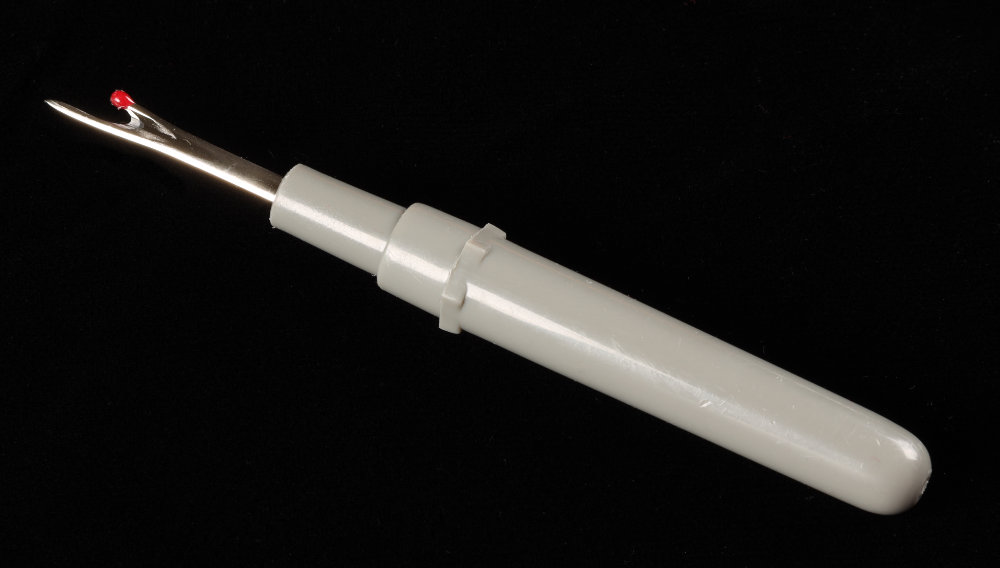
Seam Ripper
A good flexible tape measure is important to have for garment construction. First, you will need to measure your body, and that’s hard to do with a ruler or straight edge. But, also, you’ll need something light and easy to read for laying out your pattern, or measuring garment parts like seams or edges (especially for elastic).
Tape measures should last a while. But they are flexible, and with that feature comes the possibility that they will stretch over time. Older models were made of cloth and would deform faster. But even the newer ones could stretch a bit so be mindful of how you use it. When you measure your body, you want firm tension on it, but only enough to take out the slack. You don’t want to pull on it so much you cause it to stretch.
A standard dressmaker or sewing tape measure is 60″ long. Most of the time, this is perfectly adequate. You won’t need much more accuracy than 1/8″. Some have both imperial and metric measurements. And some have the numbers on both sides which is useful to just grab and measure without having to switch ends.
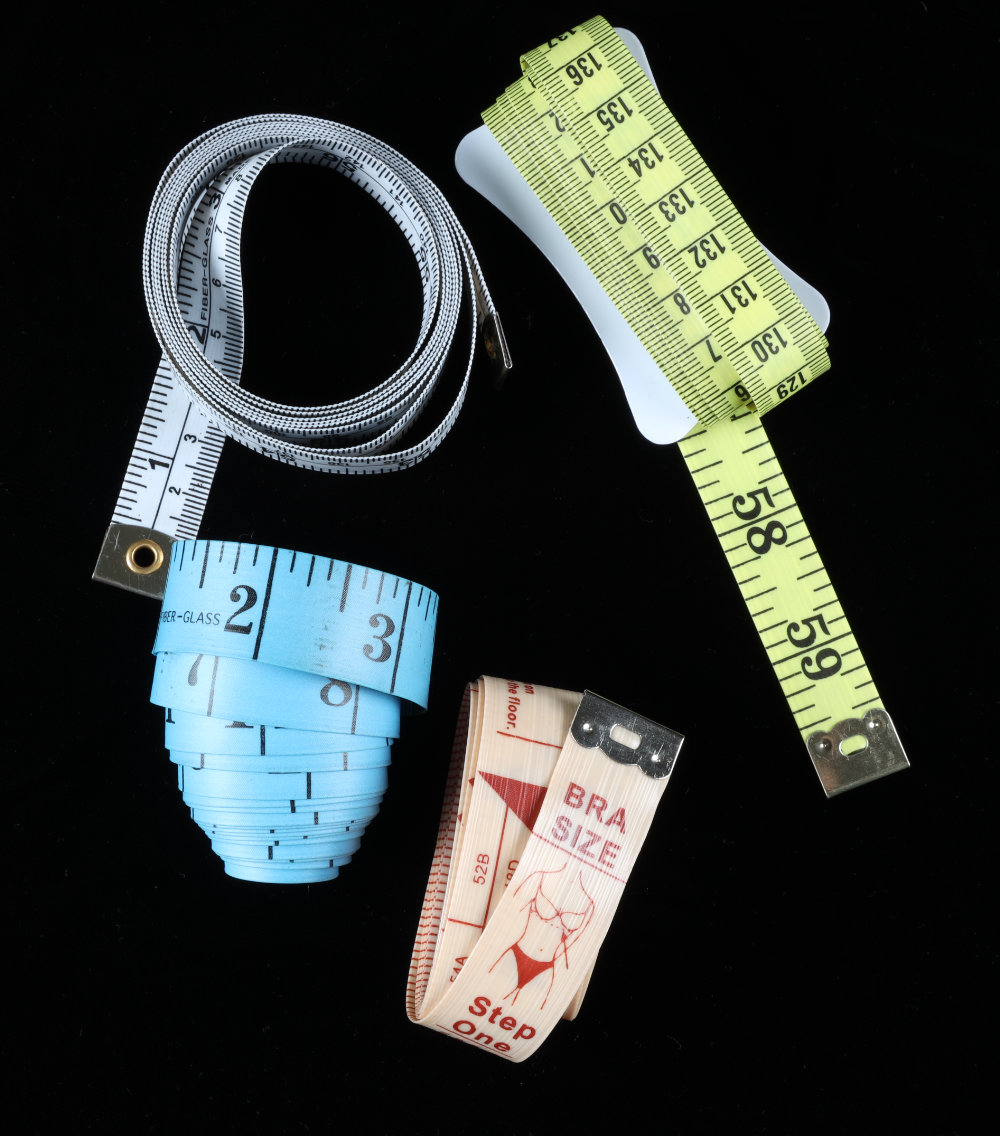
A Variety of Measuring Tapes for Sewing
Nice to Have Tools
So, beyond the 3 essential tools, here are 4 more that are pretty nice to have. This is by no means a comprehensive list of tools or notions.
Paper Scissors
You may already have a pair of scissors laying around the house that you can use for paper. And in a pinch, as stated above you can use your fabric scissors. But it is nice to know you have a less-expensive pair of scissors that you can use for paper and not have to worry about them as much.
Small Thread Snips
Scissors for Cutting Paper
Thread snips, (sometimes called nippers) are little palm sized, spring loaded scissors. They have a short blade section and are therefore, more handle than blade. They fit in the palm of your hand and are super fast for snipping threads after sewing. Because of their size and shape, they are also more efficient for snipping the threads. They are easier to wield than scissors, and therefore, more accurate when cutting. You can quite easily get super close to the fabric with these without snipping the fabric accidentally.
They are best when sharp, so as with scissors, it’s best to take care of them. Don’t Drop Them! It’s so annoying to drop scissors or nippers and get a little nick in the blade. Granted, a nick in the blade of the nippers won’t affect cutting thread on the rest of the blade, but it could prevent them from sliding correctly together to really cut well.
Needle Threader
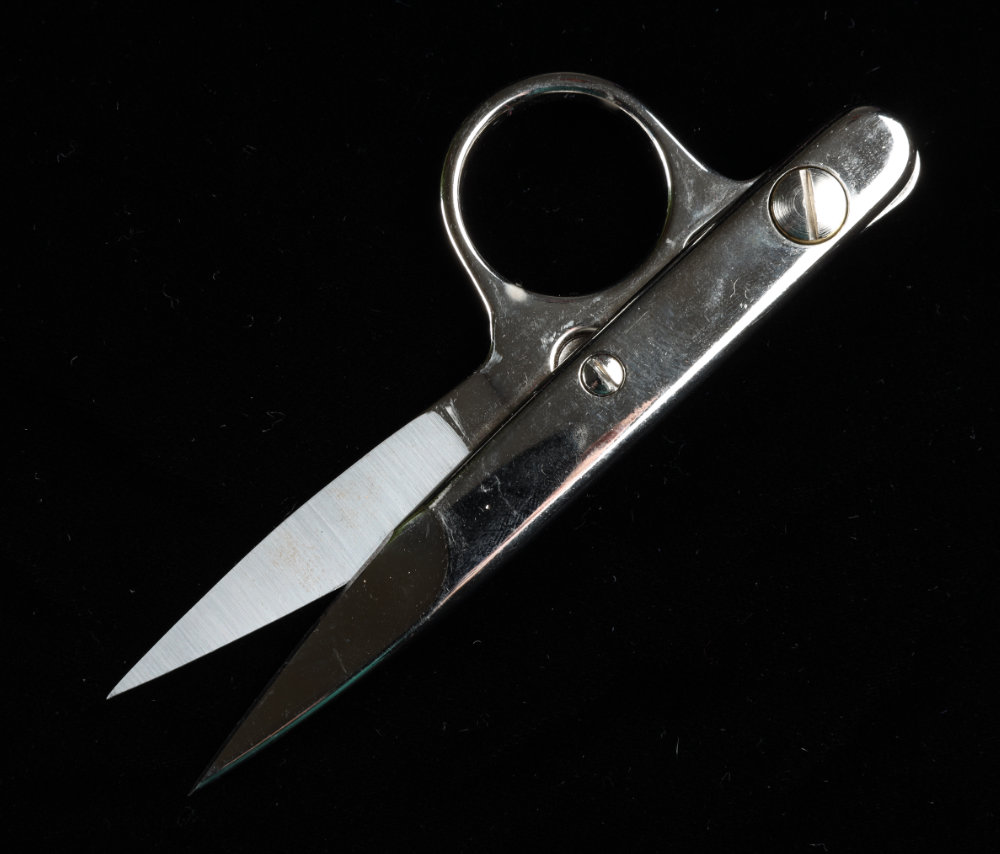
Thread Snips
A needle threader is a little loop of wire set into a handle of some sort. I’ve seen plastic and metal handles.
The idea is that the little loop of metal can more easily be poked through the eye of a needle, and then it expands to bigger than the needle hole so it’s easier to put the thread through the loop of the threader. Then, you can pull the thread through the needle.
For those of us who need “special glasses” to see up close this is an indispensable tool. It really makes threading needles so much easier. And it might be a tool you upgrade to essential.
The only real catch is that you need to push the needle threader from the back of the needle through to the front of the needle to pull the thread through from the front to the back of the needle.
Seam Gauge
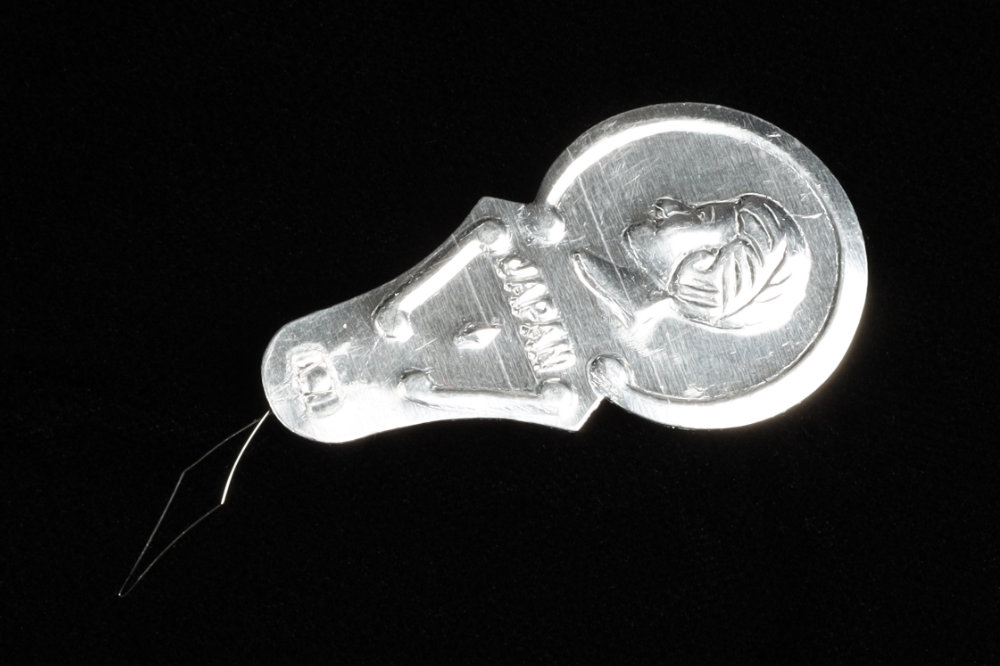
Needle Threader
The Seam Gauge is a little 6″ ruler, typically metal, with an adjustable slider on it. It’s typically used for measuring distances of things like the fold on hems, or placement of needles from the edge of the fabric for seam allowance. This comes in handy when you can move the placement of your needle left or right. It could also be used to mark the placement of buttons or button holes from the edge of a front placket of a shirt.
If you plan on sewing a lot of garments this is going to be a tool you will want sooner, rather than later.
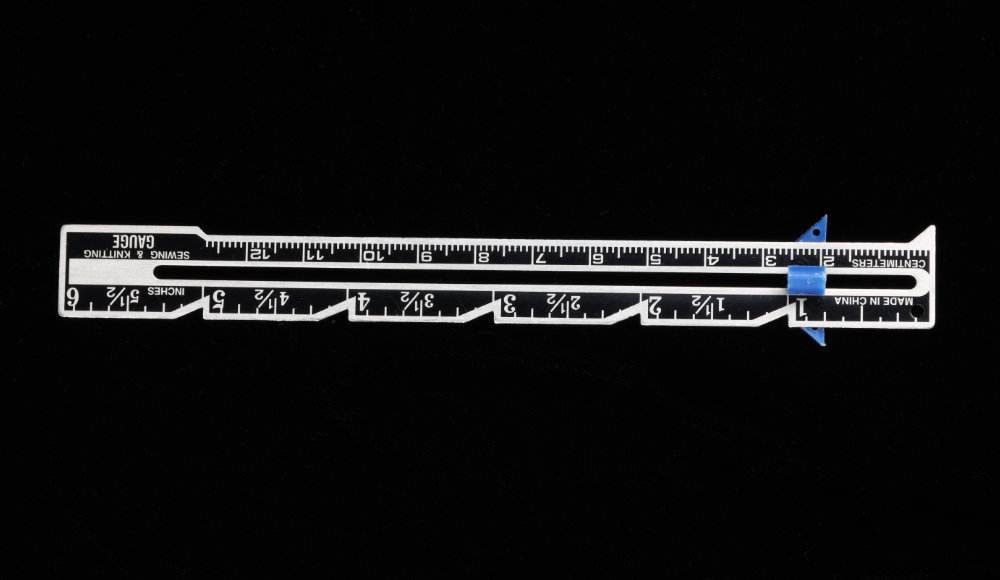
Seam Gauge
Project-Specific Tools
There are some project-specific tools that are very helpful when trying to do specific tasks. So, again, if you aren’t going to be performing some of these tasks or trying some of these techniques, you can likely skip most of these. But at some point you may want one and it’s nice to know that these exist.
Tracing Wheel
There are a few types of tracing wheels out there. If you are going to choose to mark your fabric with tracing paper (more on the paper in the consumables), you will want a wheel that has points on it. It’s been my experience, the sharper, the better, but within reason. The less pointy wheels don’t transfer the marks as easily through thicker fabrics. And that can make things challenging.
But sometimes, when you are doing some techniques, especially in pattern drafting, you want the wheel, and you don’t even use the paper.
The wheels without the points are better used for leather and waxed canvas.
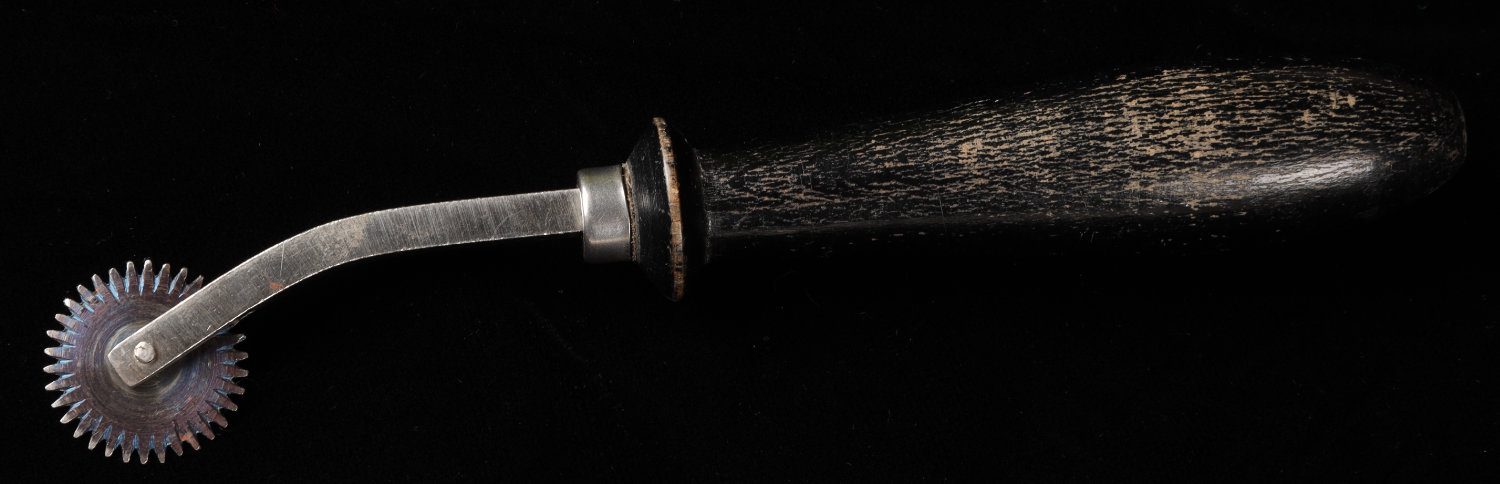
Tracing Wheel
Point Turner
A point turner is a great tool for turning sharp corners right-side out.
It’s pointy enough to poke the corner out sharp, without poking through the fabric or the corner.
Sure, you can use your scissors, but you risk harming your creation.
I use point turners for collars, cuffs, and different parts of the purses and wallets I’ve sewn.

Point Turner
Tube Turner
A tube turner is similar to a point turner, but it is made for turning longer tubes of fabric.
Essentially, there’s two pieces. One that goes inside the tube and one that stays outside. You essentially turn the tube of fabric from one to the other piece of the tube turner.
This is great if you are going to be sewing long tubes of fabric, like spaghetti straps and even wider fabric ties.
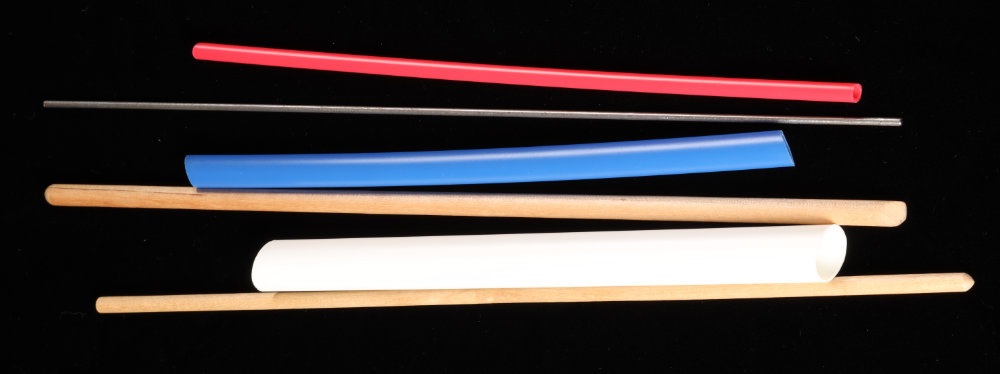
Tube Turner
Bodkin
What is a sewing bodkin? It’s a super cool tool used to thread something (elastic, string, etc) through something (waistband casing, hood drawstring casing, etc).
There are two main versions of a sewing bodkin. One clamps on the end of whatever you need to pull through. This is useful for flat-ish things like elastic. The other version is a pointy tool with a hole in the end where you’d thread whatever through it.
And yes, you can just use a safety pin. But, the thing is.. if you are stringing elastic through a waistband casing, it really helps to have a LONG safety pin (Or sewing bodkin). The longer the better, so unless you have a 4-6″ long safety pin (that can still fit through the casing and not put too big of a hole through your elastic, a bodkin will be a better bet.
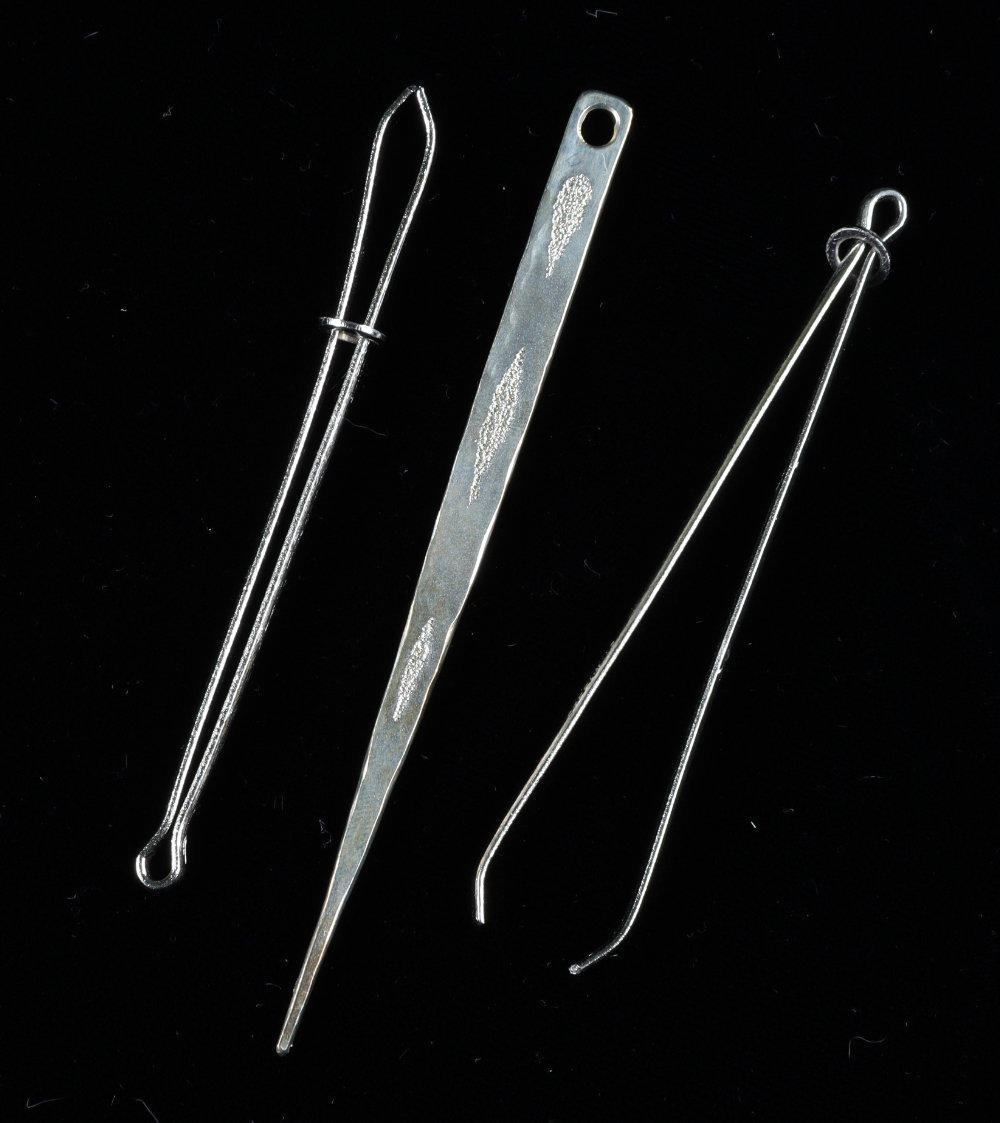
Bodkins
Clear Ruler
Clear rulers are exactly that, rulers that are clear. One of the most common is a 2″ wide ruler that is 18″ long. You can also find them wider like 6″ by 24″ which comes in handy when drafting patterns and cutting strips of fabric. Quilters also use 6 x 6 and other square ones.
They are quite useful for measuring out seam allowances and marking things on fabric. Increments of 1/8″ is fine for sewing needs.
I really don’t think I could sew without my clear rulers, but I also do a lot of pattern drafting and pattern alterations. So, if you are going to get into sewing clothes, this is pretty essential. And while I’m not a quilter, If you want to dabble in quilting, you’ll want to start getting a few of the ones favored for quilting.
I also use them a LOT when placing pockets on purses or bags and measuring for attaching straps or strap holders to bags.

18″ Clear Rulers
Consumable Notions:
Consumable notions are those little things you need to have for sewing but they get used up or worn out and need to be replenished or replaced. Some of these may surprise you because they seem like they should be on the long-lasting list but trust me, they aren’t.
Must-Have Notions
Keeping with the theme of essentials, these are things you really can’t sew without. And they wear out or get used up so you have to keep buying more.
Thread
This one is probably obvious because you need thread to sew with. And you can’t reuse it if it’s already in a project.
General all-purpose thread works well. These days, most brands have a polyester core wrapped with polyester all-purpose thread. Unless you are sewing cotton (or another natural fiber) and are going to dye it, or you’re sewing really couture stuff, you don’t need a variety of thread types. All-purpose thread works great for all of my projects.
Avoid serger thread when sewing with a sewing machine. Serger thread is actually thinner, usually, and is made so that it can have a more dense stitch. Some machines won’t even work with serger thread in the bobbin (mine won’t) so don’t be fooled by those big spools of thread for less money, you may get more headaches than you bargain for.
Likewise, you may want to avoid the super cheap threads often sold in big spools or bulk because they may be lesser quality. And that means they could break or jam more frequently.
Coats&Clark and Gutermann make good threads that I’ve personally used and have had no issues with.
You’ll want thread to match the fabric of your project. So, depending on the variety of projects you might end up with a bunch of spools of thread in different colors.
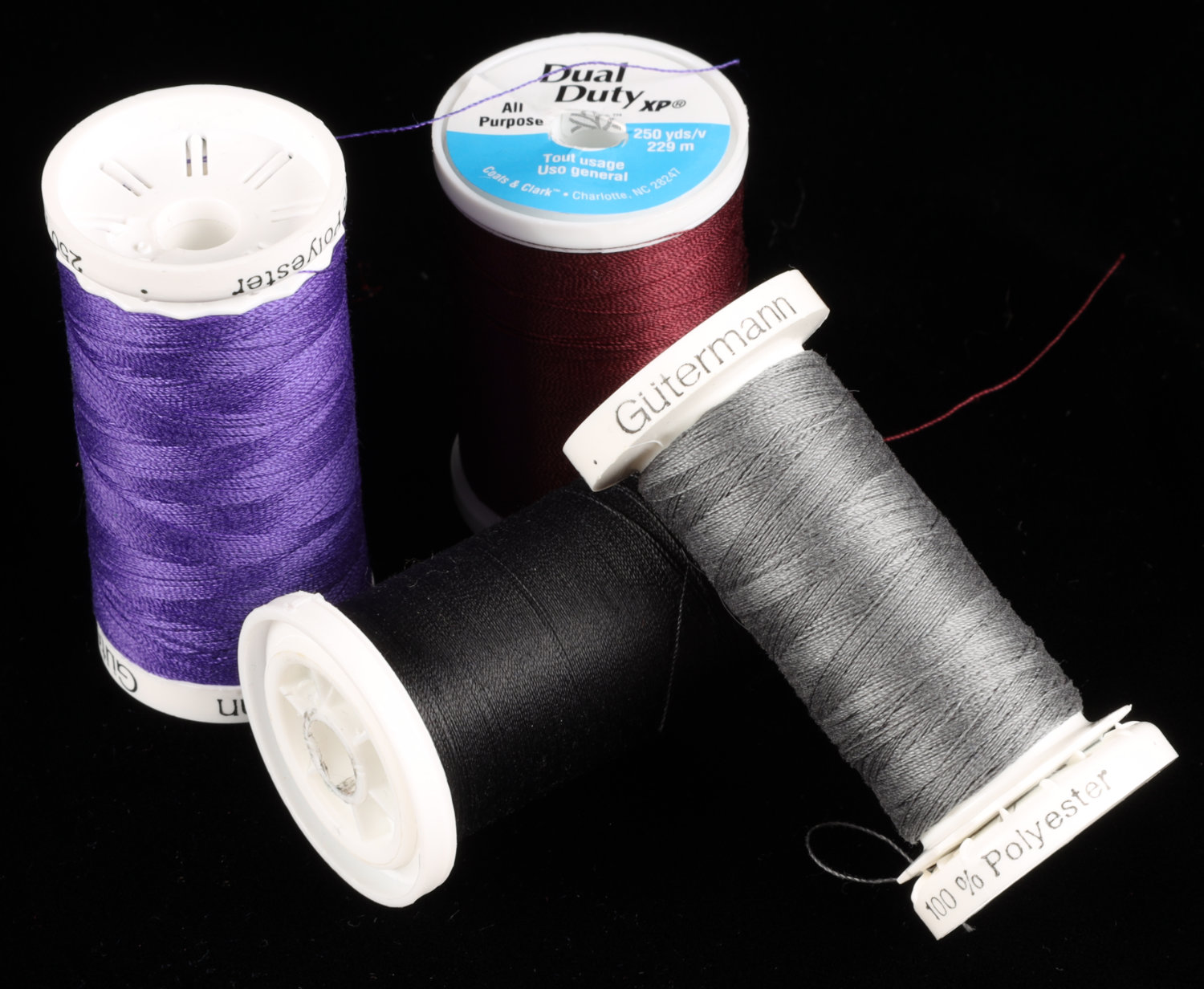
Thread
Machine Needles
This one may be more surprising. Not so much that you’ll need machine needles, but that you will need to replace them quite often.
First, you want to buy good quality needles, because cheaper ones will wear out faster.
Second, you need to match the needle to your machine. Some machines use their own branded needles and won’t work as well (or at all) if you use a more generic brand. And every needle has a shank style or specification. Not all needles work in all machines. For example, my industrial machine takes a rounded needle shank and my home sewing machine takes a needle with a flat shank. But there are even different styles of shank with flat parts so make sure you get the correct one.
Third, you need to match the type of needle to the fabric you are sewing. Sewing knits with universal needle may not work as well, as sewing woven cottons with one.
Lastly you need to match the size of the needle to the fabric and project you are sewing. Bigger isn’t always better.
As I said, needles wear out and you have to replace them. Don’t think you will save money by continuing to use a needle beyond it’s time to be tossed. Dull, damaged or bent needles can cause all sorts of problems from skipped stitches to serious machine jams that result in your project being damaged.
You will want several needles in a variety of types and sizes on hand for your projects.
As you are just starting out, you can start with a universal size 12 if you are only sewing woven fabrics or super stable knits. And if you are starting with fabric with spandex, start with a stretch needle in size 11 or 12.
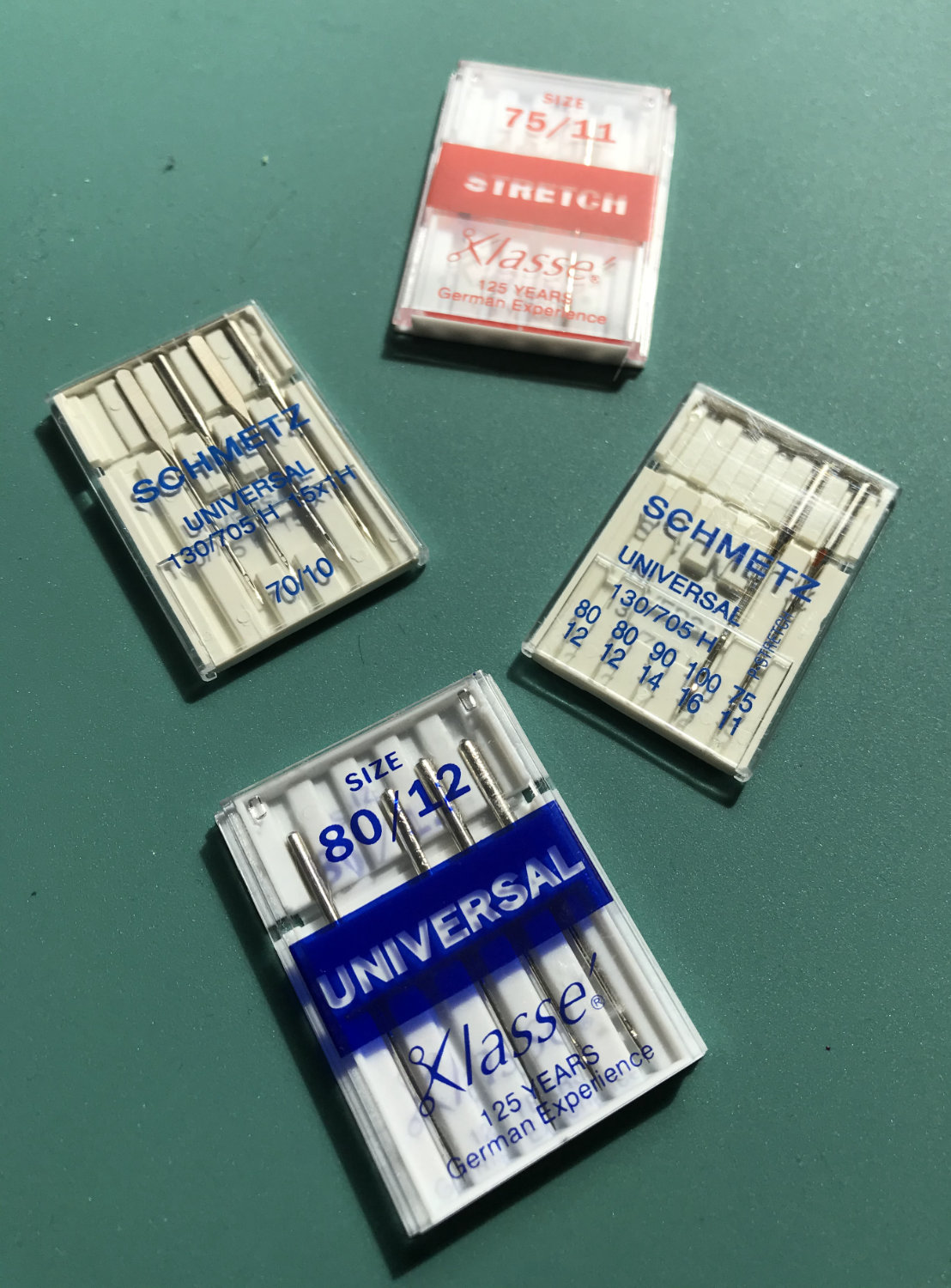
Sewing Machine Needles
Nice to Have Notions
While technically machine needles and thread are the only absolutely must haves for sewing, there are a few more notions that come really close. Especially depending on what and how you’re sewing.
Pins
For example, if you are cutting your fabric with scissors, and using a pattern, pins are quite useful to keep the pattern from moving around on the fabric while cutting it out. I’m not putting pins in the must have category simply because if you use a rotary cutter with a mat and pattern weights, you can skip pinning the pattern to the fabric. And there is such a thing as pinless sewing. And while I don’t sew everything without pins, I do tend to use them sparingly.
Regardless, pins are quite handy to have around whether you practice pinless sewing or not.
Pick the pin to go with the fabric. I love my small sharp pins because they pierce the fabric and don’t usually leave a mark.
Glass-head pins are useful because they don’t melt if you iron them. But I honestly can’t think of a time I’ve ironed a pin. Except maybe by accident.
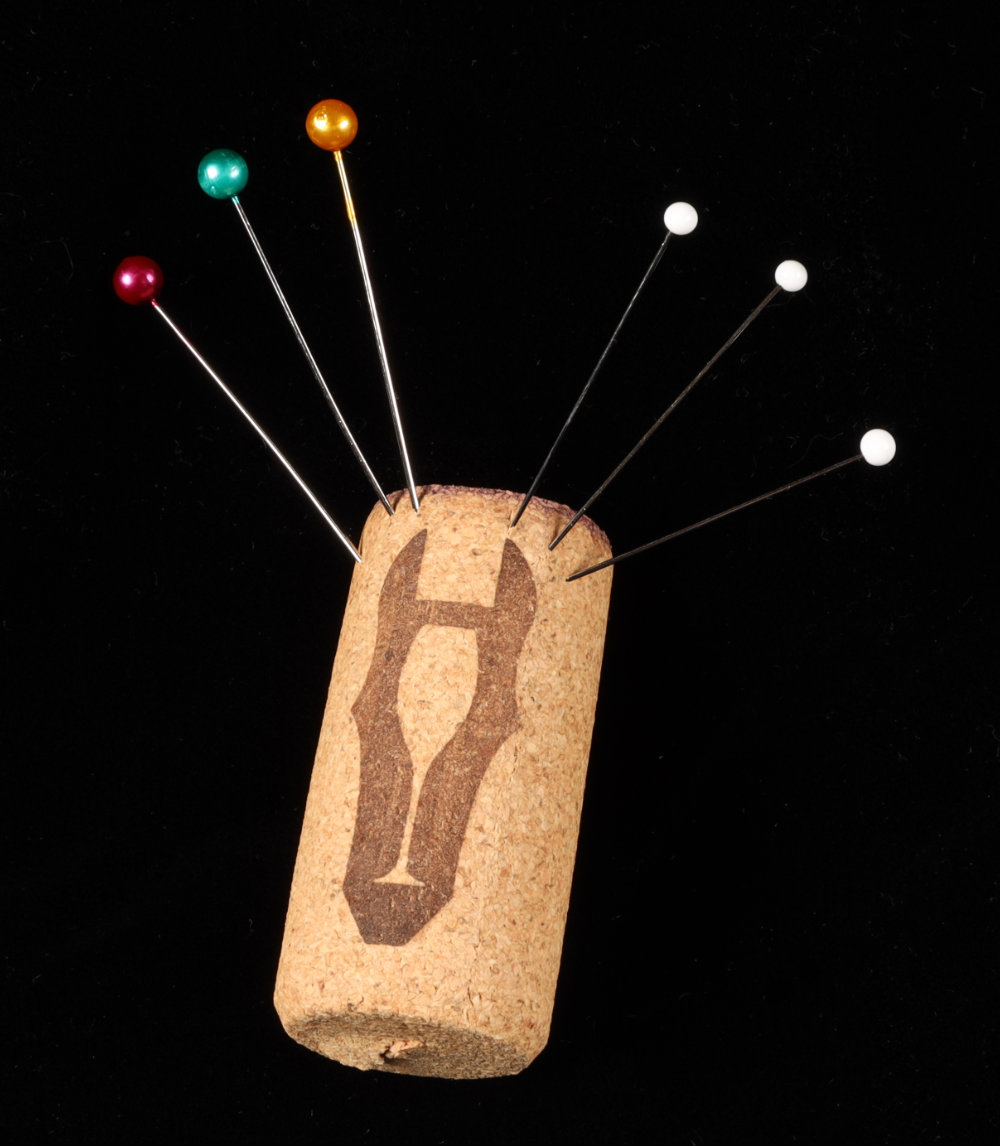
Pins
Pin Cushions
You don’t NEED to invest in a pincushion. You can store your pins in the case they come in so it isn’t necessary.
However, if you want to get one, you have a lot to choose from. (And they can make working with pins easier. AND bring some personality to your space.)
You can get the standard tomato pin cushion or a convenient option that sits on the wrist. You wear it on your wrist when sewing and it’s right there when you are removing pins while sewing.
You can also get a magnetic pin cushion. Though, they can magnetize all the pins on them and then when you pick up one, you get like 4, and then have to spend time separating them before using them. It can be annoying and time consuming. However, you may prefer this because it does make it easier to keep the pins where they should be.

Pin Cushions
Hand Sewing Needles
Some things are just easier to sew by hand, and for that you’ll want some hand sewing needles. I usually use what I inherited, because I am very impatient and don’t particularly like hand sewing. And I inherited a bunch of hand needles. But you will want to look for sharps.
Get a variety of lengths because some things work easier with slightly shorter needles and some things are easier with the longer ones.
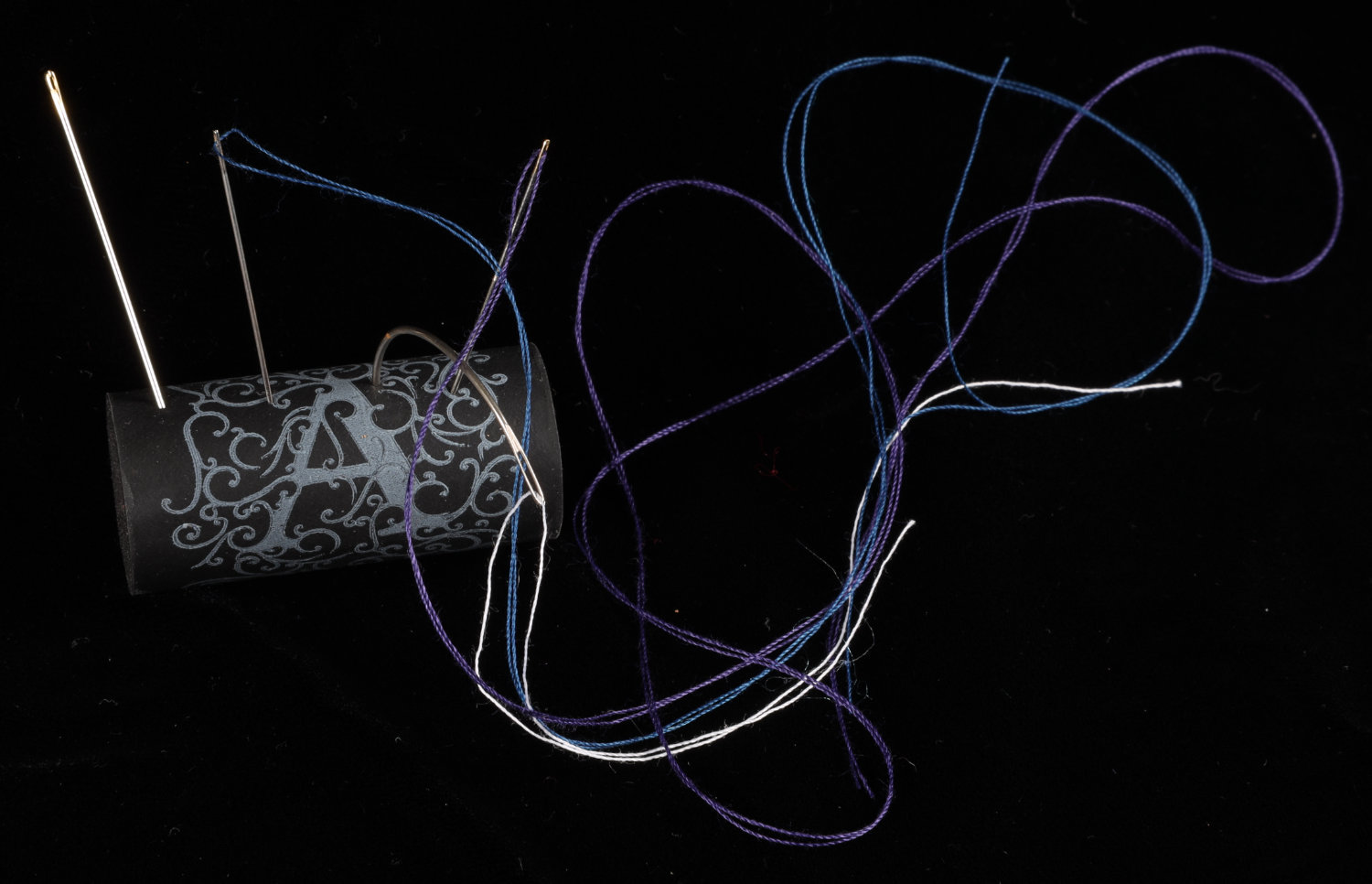
Hand Sewing Needles
Bobbins
Extra bobbins are always good to have for your machine. Having matching top and bottom threads for well-formed stitches isn’t as important as having matching thread when you are doing top stitching or edge stitching where the bobbin thread is visible. So, being able to have a set of bobbins that you can fill with all your colors is useful.
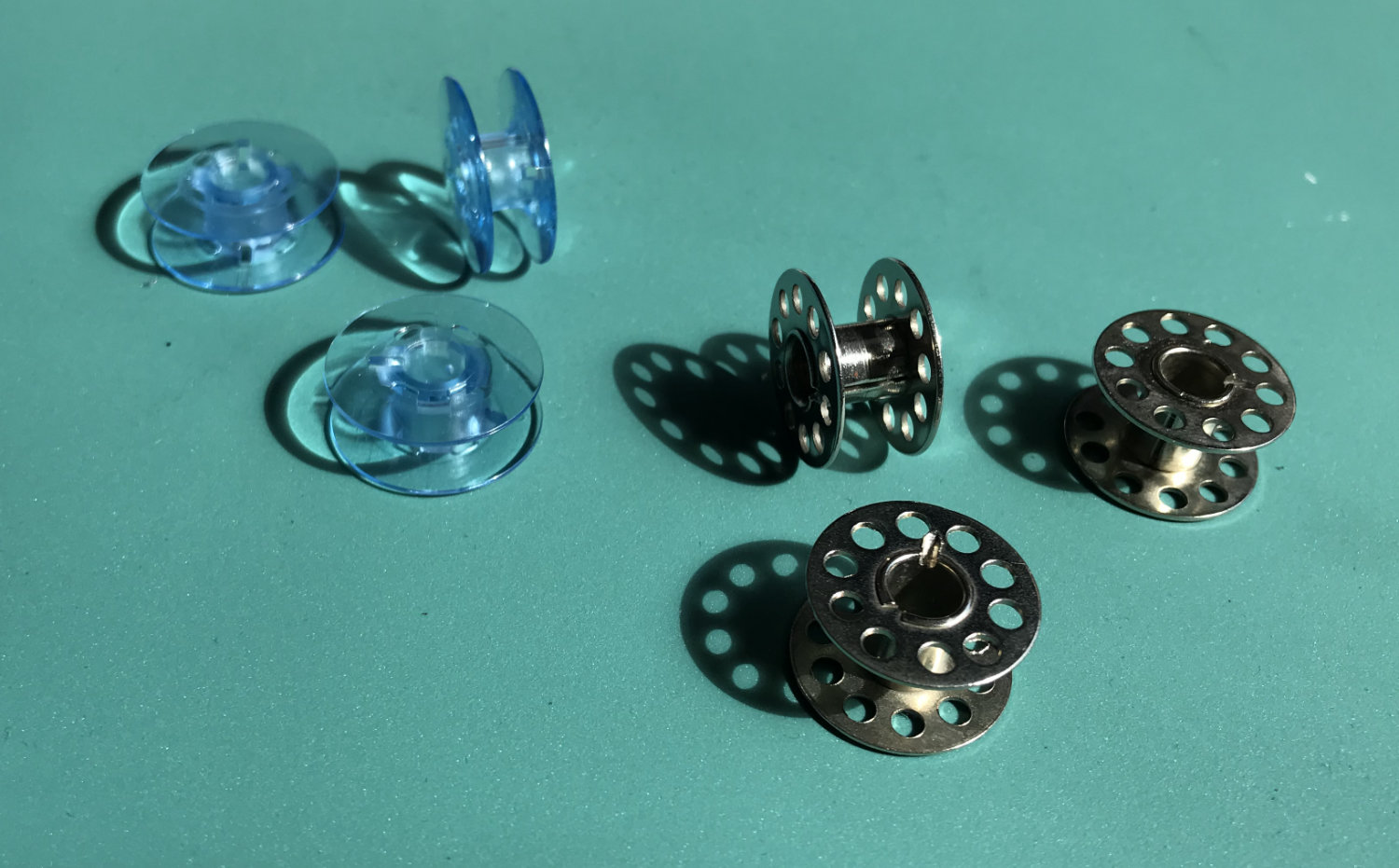
Sewing Machine Bobbins
Tracing Paper
I mentioned tracing paper when I talked about a tracing wheel. This is the kind of paper that has a color on one side that gets transferred to the paper or fabric it’s pressed against when you run the tracing wheel over it, not the kind of tracing paper one would use to trace sketches with or print out PDF Patterns.
If you are going to transfer sewing lines like for darts, or other pattern marks like the circles and squares on seam lines to fabric this is quite useful to have. It’s also useful for tracing a pattern that you haven’t cut out onto other paper.
If you are going to use it with fabric, getting a variety of colors can be useful. White and yellow often show up better on dark fabrics than red or blue. But I do have a nice red paper that I use for almost everything except red fabric.
Not all tracing paper is created equal. Some just don’t work as well as others, and some don’t wash out as well as others so if you get a dud for your use, don’t despair, and try again.
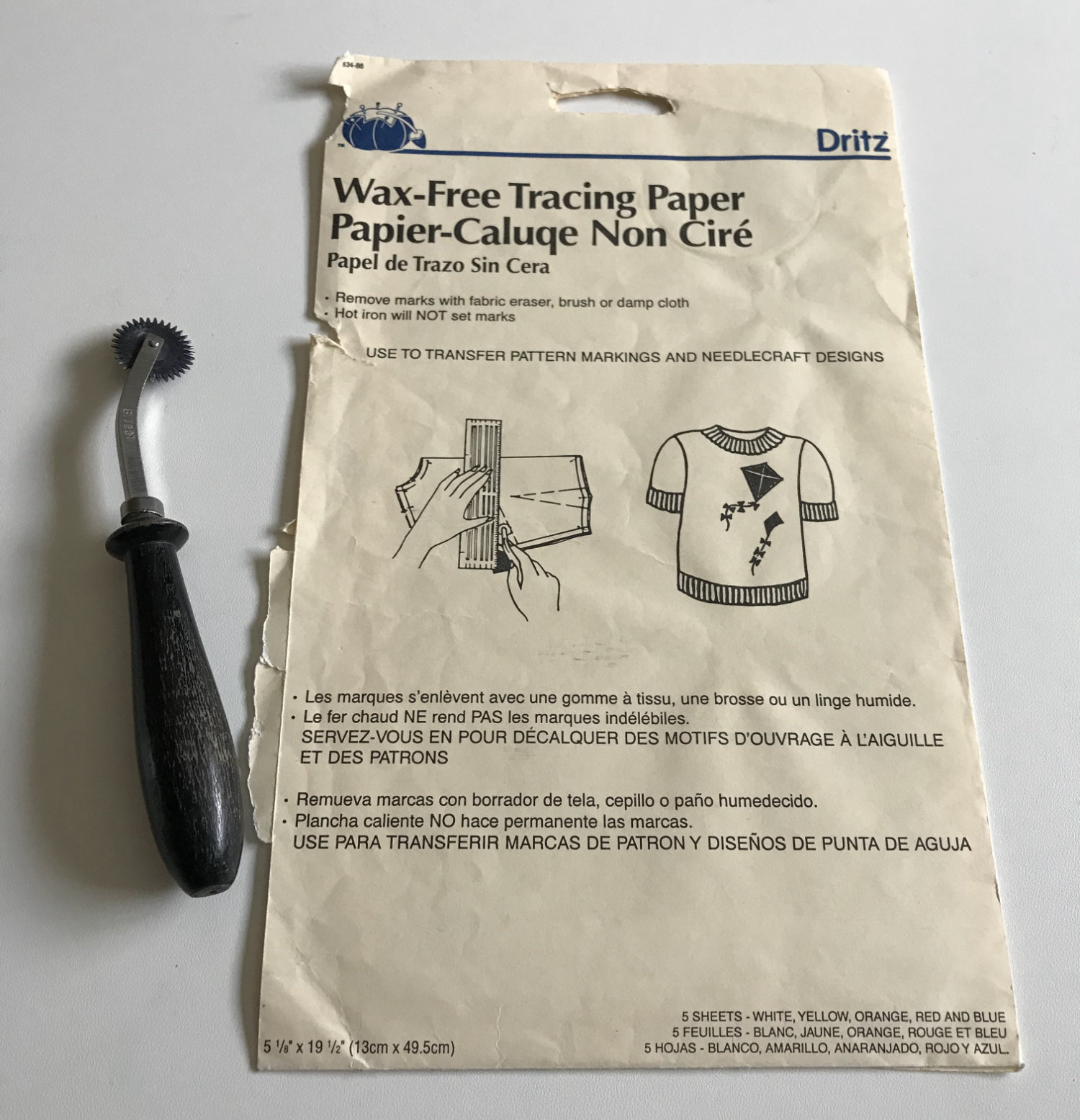
Tracing Paper (with Wheel)
Fabric Marking Tools
Beyond the tracing paper and wheel, there are a ton of marking tools for fabrics.
Personally, my favorites are chalk wheels, tailor’s chalk and erasable gel pens.
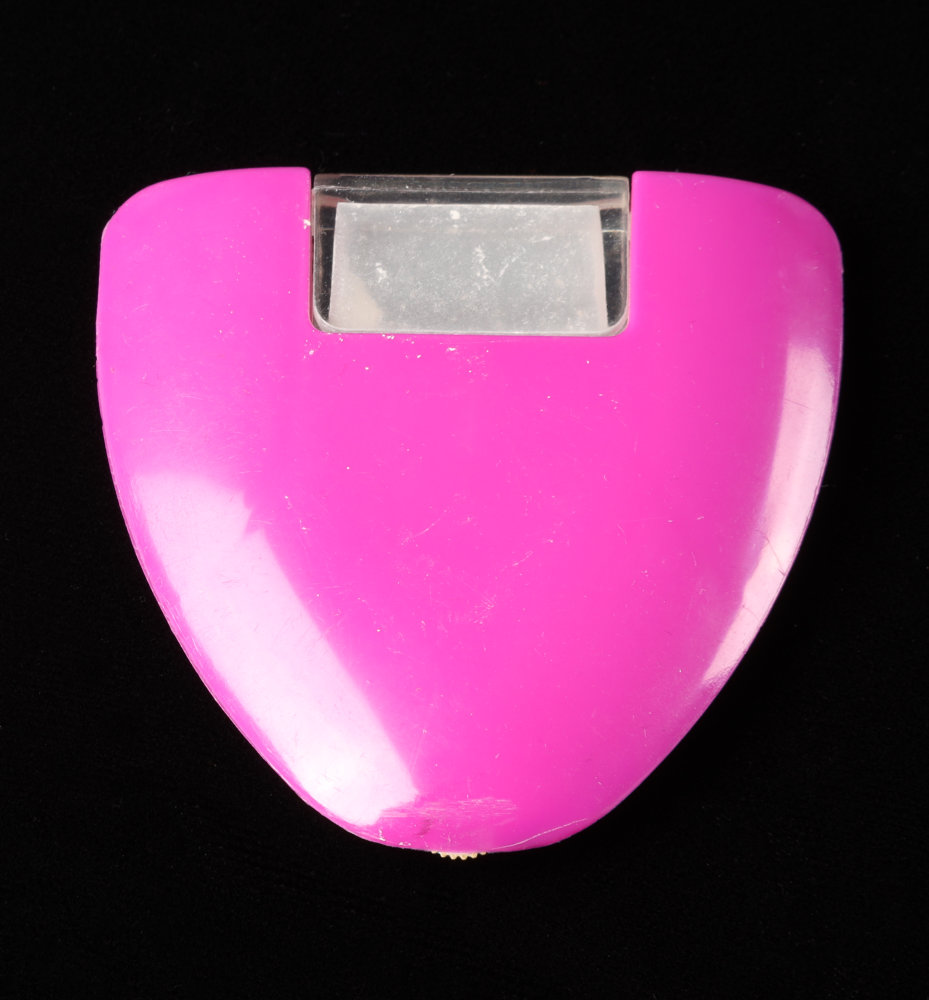
Chalk Wheel
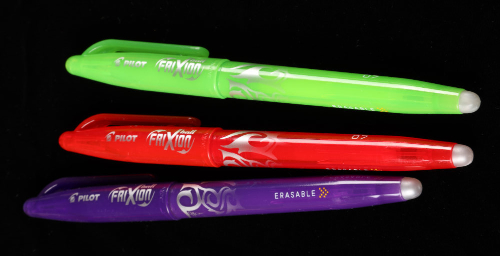
Gel Pens
There are several other notions that I have and use a lot and some things I have and use occasionally, and you are welcome to dive deeper into the world of notions with these articles:
Essential Sewing Notions for Sewing Clothes
5 Cool Sewing Notions to Make your Hobby Easier
4 Unexpected Sewing Tools You May Never Have Considered
It’s easy to get overwhelmed so only buy what you need and expand your collection as your needs grow.
Project-Specific Notions
There are project-specific notions that get used up in the project and are typically called out on the pattern envelope.
While I find myself with a collection of each of these, it’s really not necessary to have a stash of buttons, or zippers laying around waiting to be used.
Here are a few things you may see on your pattern.
Interfacing
There are several types of interfacing. You will need to pick the weight and type (woven, non-woven, or tricot) for your project based on the fabric and result you want to achieve.
And you will also need to pick how it is fastened to your fabric. There is sew-in interfacing and iron on or fusible interfacing.
For most projects that I sew these days, I prefer a medium to light weight woven fusible interfacing. It helps the fabric that it is being stuck to retain it’s appearance when it’s folded or moved around. Non-woven fusible tends to give weird wrinkles when you fold or crinkle the fabric. If you are primarily making garments, my current recommendation would be to get woven fusible interfacing.
Some accessories, like belts, do better with non-woven interfacing.
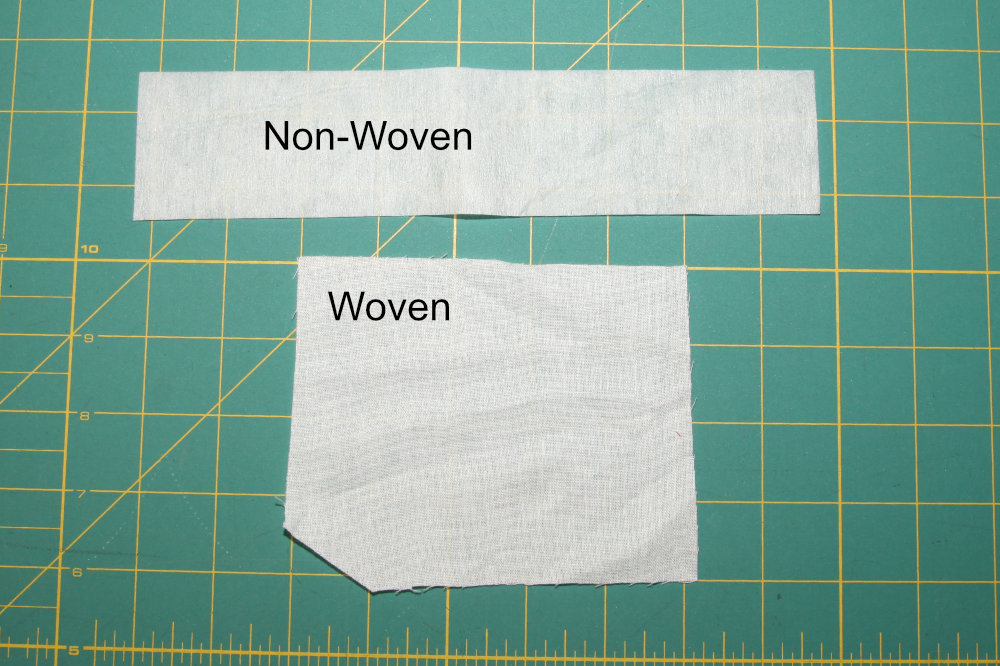
Woven and Non-Woven Fusible Interfacing
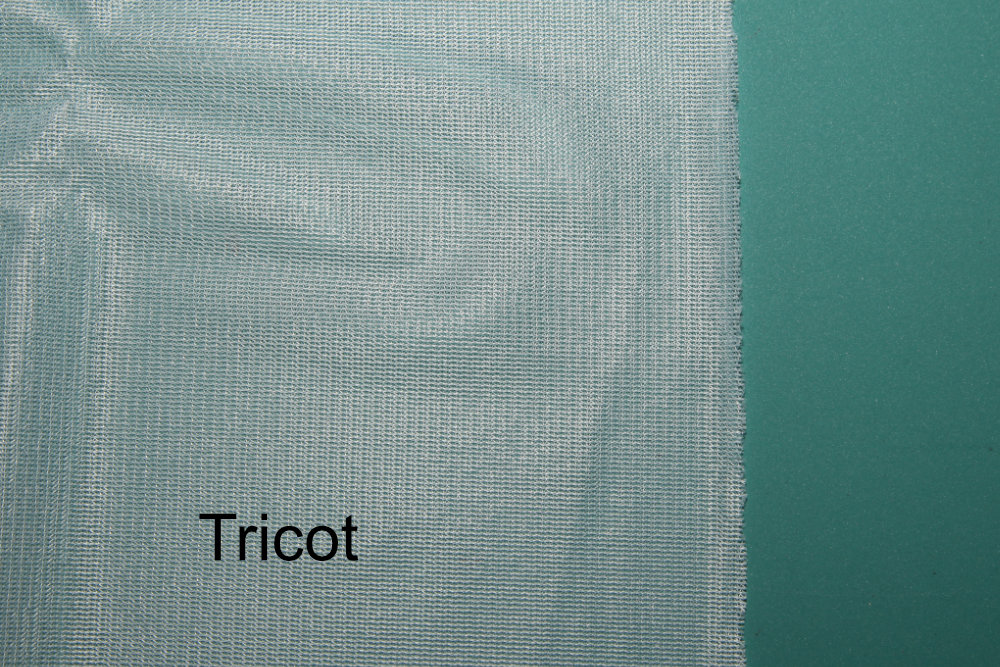
Fusible Tricot Interfacing
Buttons
Buttons come in a wide variety of sizes and shapes and even materials. If your pattern calls for buttons, they will be specified by size. This will determine the size of the buttonhole being used. Or more likely, the size of the buttonhole that is used on the pattern will determine the size of the button because sometimes you just can’t fit a bigger buttonhole.
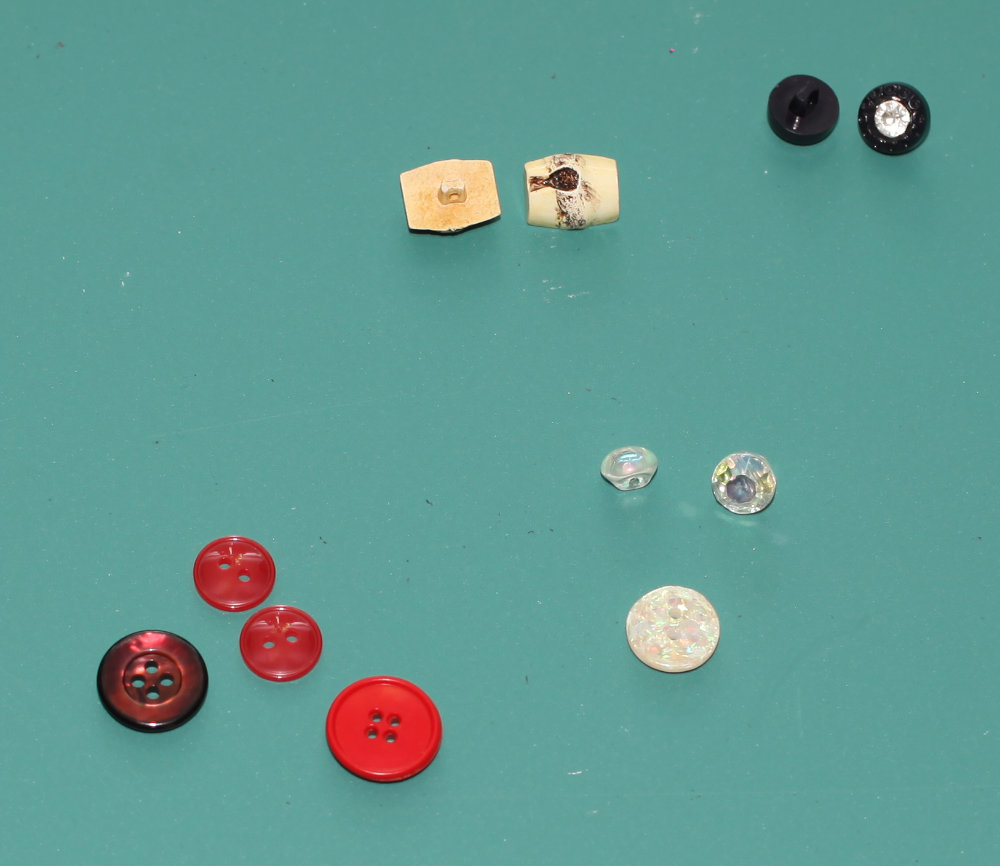
Buttons
Snaps
Snaps also come in a variety of sizes. And they have a variety of application methods, from crimping to sew-on. I’m a huge fan of the kind of snap that is crimped together. But that is a rather large investment if you are only needing one or two snaps occasionally.
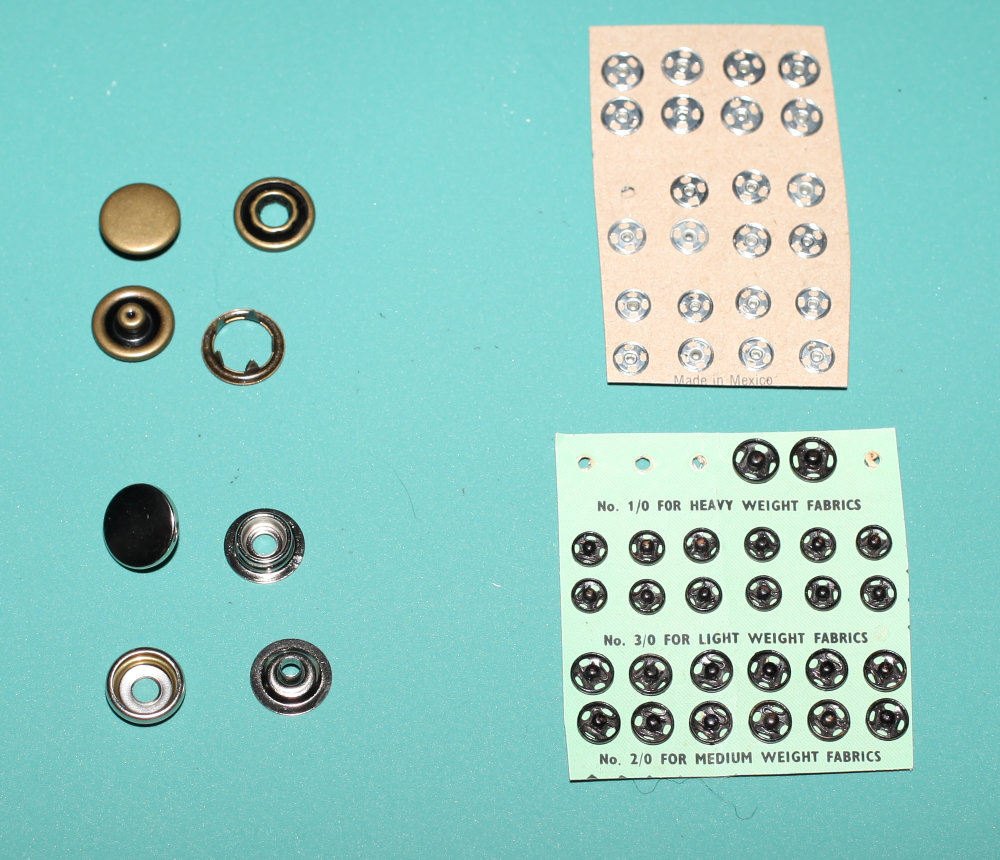
Snaps
Hooks and Eyes
Again, hooks and eyes come in a variety of sizes and even styles. There are the hooks with the loops or tiny bars for eyes. And there are flat hooks and bars typically found in trouser waistbands, and then there are hooks that are found on corsets which have a flared out shape. Most standard garments will either use the standard hook and eye, like at the top of a zipper, or the flat hook and bar like on a tab on a waist band.
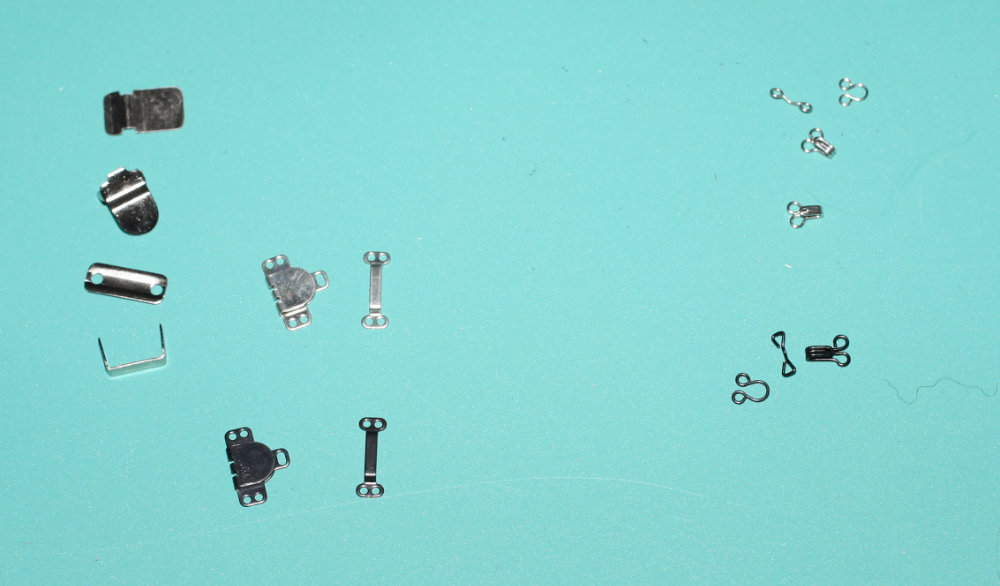
Hooks and Eyes
Zippers
Zippers might be scary to beginners. But they really shouldn’t be. Well, not all zippers should be.
There are quite a few zipper types. So, make sure you pick the correct one for your project. The patterns should call out both the length and the type (invisible, separating etc.)
But they might not call out the teeth (or coil) type. There are 3 main zipper teeth or coil types. There are metal teeth. These are common for jeans. There are molded plastic, which are super common for bags and casual jackets. And then there are nylon coil zippers. You can use nylon coil for everything from pants to bags to jackets. They are the easiest to sew and therefore are better for beginners to cut their teeth on so to speak.
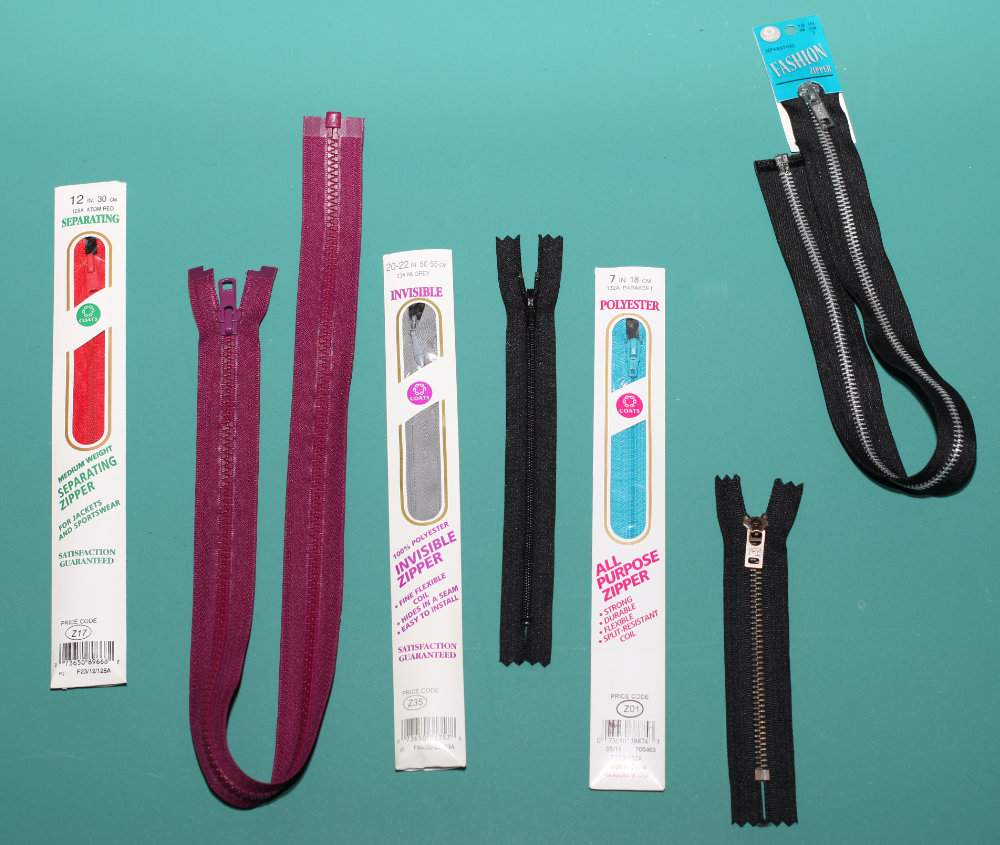
Zippers
Elastic
If your project calls for elastic most likely it will call out the width and the length of the elastic needed. Elastic comes in widths of 1/8” and up. Finding elastic that is wider than 1.5” is a little more difficult but not impossible.
You can often buy elastic in packages of pre-cut lengths, usually about a yard or so. Or, sometimes you can buy it off the spool at a specific length. Or, if you know you’re going to need a lot, you can buy the whole spool. But if you’re just starting out, that might be an excessive amount of elastic. If you are buying it off the spool at a specific length, make sure to get a little extra. It’s always easier to have too much than it is to have too little.
There are multiple kinds of elastic and some have very specific uses.
Keep in mind that most elastics have some sort of rubber inside of them for stretch and recovery and because of that they can be challenging to sew with a universal needle. If you find that your needle is pulling the rubber out of the elastic, try using a stretch needle.
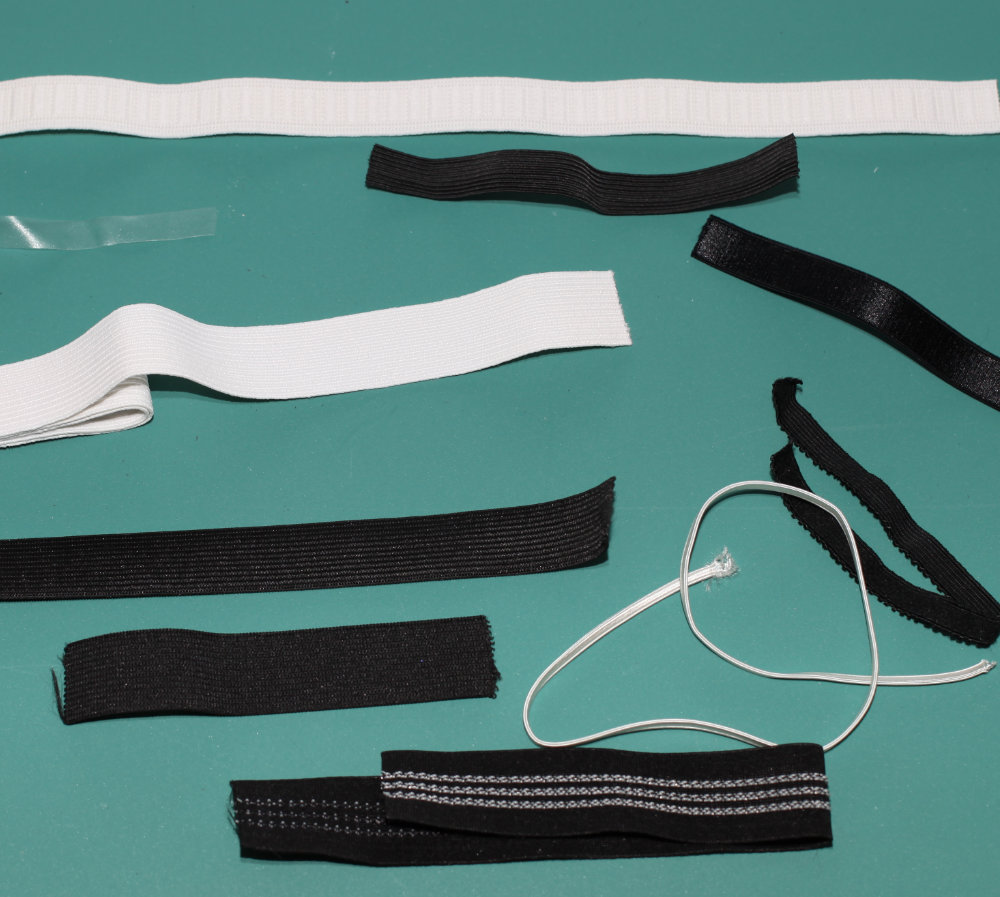
Elastic
Other Trims
Your pattern may call out anything from the above mentioned “functional” trims to decorative trims. If you are purchasing the things you need for your project in a store, and you see something on a pattern you don’t know what it is or where to find it, don’t hesitate to ask for help. If you’re shopping online, google is your friend.
Keep in mind that if you are just starting out sewing, having fewer “new” things to learn how to use or sew the better. You can build on your skills as you sew more projects.
Next Steps
Alright, now that you’ve got your shiny new tools ready to go (or at least a list of things to buy), let’s take a look at the fundamentals of a good sewing space.
It doesn’t take much to get started, but it helps to have an idea of what is needed and what to watch out for so you don’t create more problems for yourself down the road.
Up next we’ll go over some space considerations before you start. You may even want to add a few things to your shopping list. Click the button to continue.